Abstract
In today’s highly competitive business environment, it is crucial to have a sustainable operational that continuously strives for lower overall manufacturing cost. One strategy to have a lower overall manufacturing cost is to reduce product failure by developing the ability to predict production flaws at the earliest possible stage alongside the entire value-added stream since it can reduce expensive trial and error attempts at the real manufacturing floor. This doctoral thesis focuses on investigating major imperfection in coupled processes of Welding-to-Forming and Forming-to-Welding which are frequently found in parts production in automotive industries. Finite Element Method (FEM) - based Virtual Manufacturing (VM) approach is used to predict final dimensional change in both welding and forming processes through the utilization of specialized software Simufact.Welding and Simufact.Forming. This research is to demonstrate the accuracy in predicting final geometry in both coupled processes where the physical properties from the first process serves as the initial condition for the later process. The results will be compared to the experimental results to verify its level of accuracy in predicting the imperfection which was executed by utilizing thermo-mechanical FEM under consideration of non-linear isotropic hardening and strain rate. For verification purpose, experimental butt-joint welding was joined by means of robotic welding system (ABB IRB 2400/16) and advanced power source (KEMPPI Pro-EvolutionProMig) with mixed shielding gas 80% Ar/ 20% CO2 as well as filler wire ER70S. Experimental forming process on sheet metal was carried out using (SUNFLUID 800/2007) bending machine. Low carbon steel S235 with thickness of 2 mm is selected as material for both simulation and experiment since this type of steel is the most commonly used material in automotive spare part production due to its excellent ductility and toughness. The study shows in experimental result on coupled processes of Welding-to-Forming, that the average final displacement due to spring-back effect is 2.24 mm, while on Forming-to-Welding experimental results, the average final distortion yields the value of 1.12 mm. The FEM-based VM result, on the other hand, indicated that for the coupled processes Welding-to-Forming the error range on final displacement is found out to be 6.25% in average. In the case of coupled processes Forming-to-Welding, the error range on final distortion yields the error value of 11.61% in average. It can be concluded that coupled process Forming-to-Welding is the better coupled process compared to Welding-to-Forming since it yields a smaller average value of geometrical change. The range of error was caused by non-uniformly distributed geometrical change across the specimen after welding and forming processes. However, in both coupled processes the errors are all still within acceptable engineering level.
Metadata
Item Type: | Thesis (PhD) |
---|---|
Creators: | Creators Email / ID Num. Ishak, Dendi Prajadhiana 2013226542 |
Contributors: | Contribution Name Email / ID Num. Thesis advisor Manurung, Yupiter Harangan (Prof. Ir. Dr. -Ing. Ts.) UNSPECIFIED |
Subjects: | T Technology > TA Engineering. Civil engineering > Engineering mathematics. Engineering analysis > Finite element method |
Divisions: | Universiti Teknologi MARA, Shah Alam > College of Engineering |
Programme: | Doctor of Philosophy (Mechanical Engineering) |
Keywords: | Virtual manufacturing; Finite Element Method (FEM); Welding Process and Distortion Theory; metal forming |
Date: | June 2021 |
URI: | https://ir.uitm.edu.my/id/eprint/60730 |
Download
![[thumbnail of 60730.pdf]](https://ir.uitm.edu.my/style/images/fileicons/text.png)
60730.pdf
Download (36kB)
Digital Copy
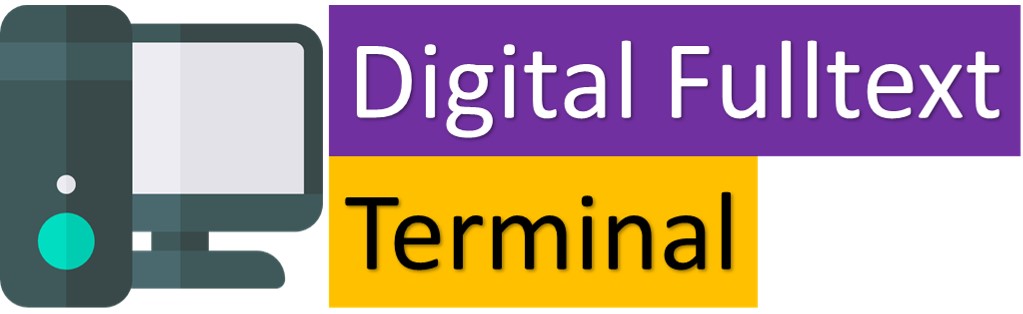
Physical Copy
ID Number
60730
Indexing
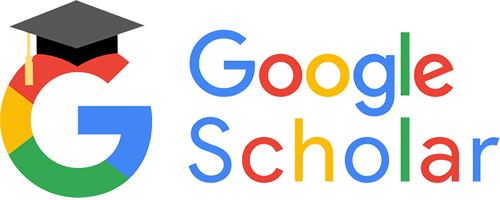
