Abstract
Three dimensional (3D) printing or additive manufacturing is a process of creating or manufacturing solid objects which is in three dimensional from a digital file. The additive process is used to achieve the creation of a 3D printed object. In this process, any object is created by laying down many successive layers of material until the object is formed. Before the process of 3D printing, three manipulating variables were determined and set which are the infill density (%), printing speed (mm/s) and temperature of hot end (°C). The Catia design - a dog bone design based on American Society for Testing and Materials (ASTM) D638 Type IV was used with the help of the Creality Ender 3 3D printer. The process of printing the (ASTM) D638 Type IV begins once all three parameters involved have been determined and confirmed. The Response Surface Methodology (RSM) in Minitab was used for the Design of Experiment (DoE). It maximise the production of a special substance by optimization of operational factors. The tensile strength of the printed object was tested by using the Tensile Testing machine. From the experiment, infill density and printing speed give the most influence parameter towards ultimate tensile strength while infill density affects the fracture strength mostly. The optimum plot for ultimate tensile strength is 100% infill density, 30 mm/s printing speed and 250°C. The fracture strength results were not taken in this project since it is not reliable.
Metadata
Download
![[thumbnail of 37781.pdf]](https://ir.uitm.edu.my/style/images/fileicons/text.png)
37781.pdf
Download (47kB)
Digital Copy
Physical Copy

ID Number
37781
Indexing
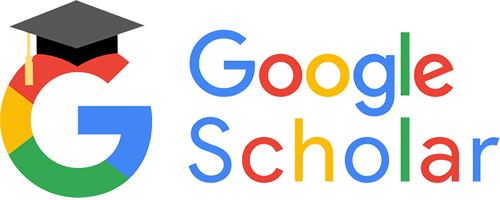
