Abstract
There are a few thousands commercial aircrafts operating today. Many of those
aircrafts are considered old or aging and will experience damages whether little or
large. Damages in aircraft structures are classified as negligible a~d intolerable.
Since commercial aircrafts are constructed to be in Damage Tolerant Design (DTD),
negligible damage is not threatening and the aircraft can still operate under some
limitations. Intolerable damage however, should be repaired to prevent growth of the
damage and to maintain airworthiness of the aircraft. One of the damages that is
covered in this research is a crack damage and the repair on it. The damage location
in this research is on the skin next to the top hat stringer section on a stiffened panel.
The case study simulated the rear fuselage stiffened panel of a Boeing 737. Most
damage repair methods and procedures are prescribed in the Structural Repair
Manual (SRM). The SRM provides details procedures of repair using bolts and
rivets. The damage case in this research is not part of the SRM. Eyen though
extensive stress analysis has been done by the manufacturer before the repair
procedure is documented, however, there is no strength analysis reported in the
SRM. This research conducted a stress analysis on the structure before damaged,
after damaged, and after repaired conditions, in which riveted patch was used in one
case, and bonded patch in the other. Two methods of analyses were conducted
namely finite element analysis using ANSYS software, and experimental method
using strain gages and Universal Testing Machine. The stress distributions of all
conditions were compared between the finite element and the experimental methods.
In addition to the above, theoretical analysis was used to predict the static strength of
the structure all four conditions. The static strengths of all conditions were compared
between theoretical and experimental methods. It was expected that both repair
methods would restore the original strength of the structure. Based on the
comparison between FEA and experimental results, there were agreements on the
graph pattern. However, there were extreme values in the readings of the strain gages
near the jigs or load application points. This was mainly due to the $etting of the jigs
which produced local effect high stress area. Based on the static strength· analysis, it
was found that the riveted patch repair was weaker than the original condition by
15%. The bonded patch repair failed at more than 20% less than the original strength.
This was due to the limited resources of bonding repair facilities which made the
bonding process not properly done so that the patch· was not perfectly bonded to the
skin.
Metadata
Item Type: | Thesis (Masters) |
---|---|
Creators: | Creators Email / ID Num. Ramly, Ramzyzan UNSPECIFIED |
Subjects: | T Technology > TJ Mechanical engineering and machinery > Mechanics applied to machinery. Dynamics T Technology > TL Motor vehicles. Aeronautics. Astronautics > Aeronautics. Aeronautical engineering > Aircraft |
Divisions: | Universiti Teknologi MARA, Shah Alam > Faculty of Mechanical Engineering |
Keywords: | Stiffened panel stress analysis, crack damage, riveted patch repair, bonded patch repair, finite element analysis, experimental analysis, static strength |
Date: | 2005 |
URI: | https://ir.uitm.edu.my/id/eprint/3689 |
Download
![[thumbnail of TM_RAMYZAN RAMLY EM 05_5 1.pdf]](https://ir.uitm.edu.my/style/images/fileicons/text.png)
TM_RAMYZAN RAMLY EM 05_5 1.pdf
Download (293kB)
Digital Copy
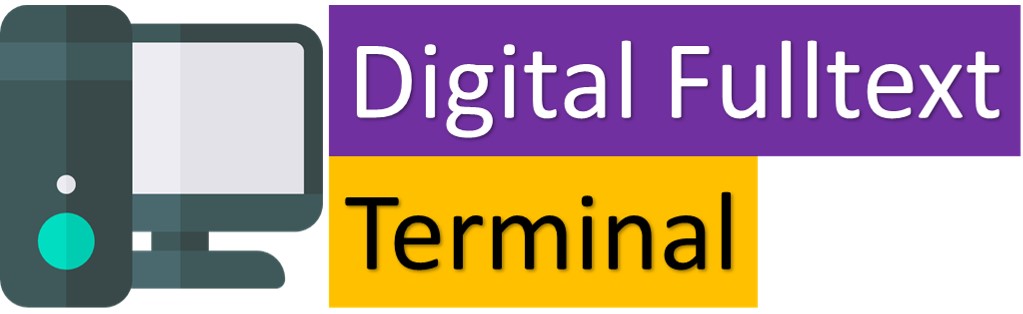
Physical Copy
ID Number
3689
Indexing
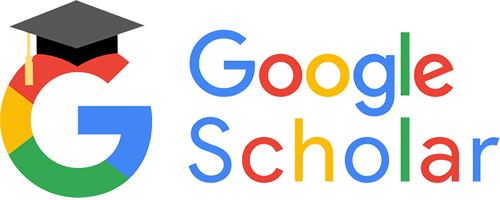
