Abstract
The research in Copper based friction materials is mostly focused on the effect of material composition on its mechanical and tribological characteristics, while the information of the optimization of composition and fabrication process is limited. This research is to optimize the material composition which composed of copper, iron and carbon. Six samples composed of copper, iron and carbon were fabricated through powder metallurgy process. One formulation is using commercial carbon while the other five formulations are using activated carbon from palm kernel shell as its carbon content. The research begins with sample preparation using powder metallurgy process as follows; (i) mixing, (ii) compacting, (iii), sintering. The sintering process took place in a tube furnace under pure nitrogen atmosphere at a temperature of 960°C for 1 hour. The effect of carbon from palm kernel shell and copper on friction and wear, hardness, porosity, and specific gravity properties were examined using international standard test procedures. Test results signify that the formulation using activated carbon from palm kernel shell can replace the available commercial carbon where it produces higher coefficient of friction (COF). Sample NA1 composed of 85 wt. % of copper, 12 wt. % of iron, and 3 wt. % of activated carbon from palm kernel shell is the optimized formulation where it produced the highest COF as well the Shore D hardness. Detail analyses on the mechanical and tribological test result show that there is no direct correlation between the mechanical with tribological properties.
Metadata
Download
![[thumbnail of 35082.pdf]](https://ir.uitm.edu.my/style/images/fileicons/text.png)
35082.pdf
Download (103kB)
Digital Copy
Physical Copy

ID Number
35082
Indexing
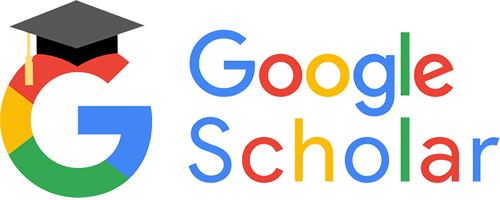
