Abstract
Accurate analytical models of engineering structures are of paramount importance for dynamicists to be used in predicting the dynamic behaviour of the structures. The finite element method (FEM) and the experimental modal analysis (EMA) have been known as powerful and useful methods that can be used to determine the dynamic behaviour of the structures. However, it is very difficult and challenging to accurately model large complex structures that are often found to be a combination of the different types of joints. Previous work has revealed that, spot welds tend to present the local issues such as thermal effects, initial stresses, diameters of the spot welds, contacting areas, etc. to the structure. They have been discovered to be very difficult to be accurately modelled using analytical methods which are one of them is the finite element method. Therefore, in order to have a reliable finite element model of a structure, measured data obtained from the experimental modal analysis can be integrated with analytical data to reconcile the finite element model and the procedures involved in the reconciliation is a model updating process. The model updating methods, in general, are classified into two main different groups which are the modal based updating and frequency response function (FRF) based updating. This research was aimed to investigate the accuracy, efficiency and economics of the frequency response function (FRF) based updating method in updating the finite element model of a structure with laser spot welds. The physical test specimen used in this work is a structure consisting of a squared thin plate (110mm x 564 mm) and a hat shape plate. They were assembled together with twenty laser spot welded joints. In this study, the measured and predicted results of the structure were obtained from the experimental modal analysis (EMA) and finite element analysis using MSC Software (Nastran/Patran). The structure was tested under free-free boundary conditions using impact hammer testing and roving accelerometers in order to measure its FRFs. The initial finite element model of the welded structure was constructed using three different element connectors (RBE2, ACM2 and CWELD) and the three different models were then used to predict the FRFs of the structure. The comparison of the initial results revealed that the CWELD based FE model of the welded structure has showed better capability to represent the laser spot weld joints in the physical test structure with the total error recorded was 12.35 percent as compared to the ACM2 based FE model (13.42 percent) and the RBE2 based FE model (77.80 percent). The initial CWELD based FE model was then used as a benchmark model in the FRF based updating method. The attempts at updating the initial CWELD based FE model of the welded structure using the FRF based updating method have been numerically and experimentally proved with a satisfactory acceptable level of achievement. The predicted results obtained from the updated CWELD based FE model have shown a great improvement with 53.14 percent of reduction in the total error computed from the initial CWELD based FE model. In conclusion, FRF based updating method has been successfully used in increasing the quality of the predicted finite element FRFs over the measured counterparts.
Metadata
Item Type: | Thesis (Masters) |
---|---|
Creators: | Creators Email / ID Num. Mohd Zin, Mohd Syazwan UNSPECIFIED |
Contributors: | Contribution Name Email / ID Num. Thesis advisor Abdul Rani, Muhamad Norhisham UNSPECIFIED |
Subjects: | T Technology > TS Manufactures > Metal manufactures. Metalworking > Welding |
Divisions: | Universiti Teknologi MARA, Shah Alam > Faculty of Mechanical Engineering |
Programme: | Master of Science (Mechanical Engineering) |
Keywords: | FRF, laser, welded |
Date: | 2018 |
URI: | https://ir.uitm.edu.my/id/eprint/79332 |
Download
![[thumbnail of 79332.pdf]](https://ir.uitm.edu.my/style/images/fileicons/text.png)
79332.pdf
Download (195kB)
Digital Copy
Physical Copy

ID Number
79332
Indexing
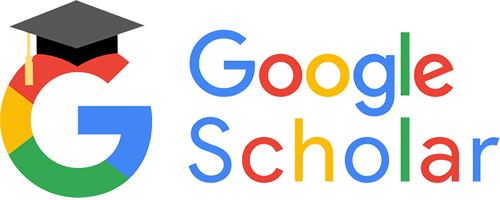
