Abstract
Stainless steel 304 (SS304) is one of the widely used steel fasteners in both commercial and industrial sectors. However, stainless steel is susceptible to failure in a harsh corrosive environment despite its good corrosion resistance. Nowadays, the electrodeposition process is gaining traction as a flexible method to improve surface properties using various types of alloys. In this study, Co-Ni-Fe alloy was chosen as a protective coating for SS304 bolts through electrodeposition process. The purposes of this research are to develop a better understanding on the surface properties of Co-Ni-Fe thin film deposited onto stainless steel 304 bolt and the corrosion behaviour in corrosive mediums taken from actual environments. First, the coatings were synthesised with deposition time of 15, 30, and 45 minutes and current density of 28, 35, and 42 mA/cm2 whereas the other plating parameters were kept constant. The samples were characterised using scanning electron microscope (surface morphology and elemental composition), 3D surface metrology system (roughness and thickness), and hardness testing machine (microhardness). In most cases, there was a correlation between the trends of surface roughness and corrosion rate. Both properties had lower values as deposition time increased. In order to select the best combination of plating parameters for environmental tests, the samples were further analysed with potentiodynamic polarisation technique using a potentiostat to obtain the corrosion rates. The optimum plating parameters were 30 minutes and 42 mA/cm2 because the corrosion rate was the lowest. More samples were produced using these optimum parameters for the environmental immersion test, which consisted of river water, tap water and seawater. River water was the most aggressive environment because the samples lost the highest weight followed by seawater and tap water during the weight loss analysis. Electrochemical impedance spectroscopy (EIS) results indicated that the impedance |Z| value varied as immersion period increase. River and tap water had an increasing |Z| value whereas seawater had a decreasing |Z| value over times. In terms of electrochemical aspects, river water caused the highest corrosion rate whereas the weight loss test showed that seawater caused the highest corrosion rate. It did not had direct relationship with weight loss trend. Based on these environmental tests, the corrosion resistance of Co-Ni-Fe coating is the highest in tap water, followed by river water and seawater.
Metadata
Item Type: | Thesis (Masters) |
---|---|
Creators: | Creators Email / ID Num. Md. Nor, Muhammad Syafiq 2018457108 |
Contributors: | Contribution Name Email / ID Num. Thesis advisor Salleh, Zuraidah UNSPECIFIED |
Subjects: | T Technology > TA Engineering. Civil engineering > Materials of engineering and construction > Physical properties T Technology > TA Engineering. Civil engineering > Materials of engineering and construction > Metals |
Divisions: | Universiti Teknologi MARA, Shah Alam > College of Engineering |
Programme: | Master of Science (Mechanical Engineering) |
Keywords: | Bolts, effects, coated |
Date: | 2022 |
URI: | https://ir.uitm.edu.my/id/eprint/77964 |
Download
![[thumbnail of 77964.pdf]](https://ir.uitm.edu.my/style/images/fileicons/text.png)
77964.pdf
Download (186kB)
Digital Copy
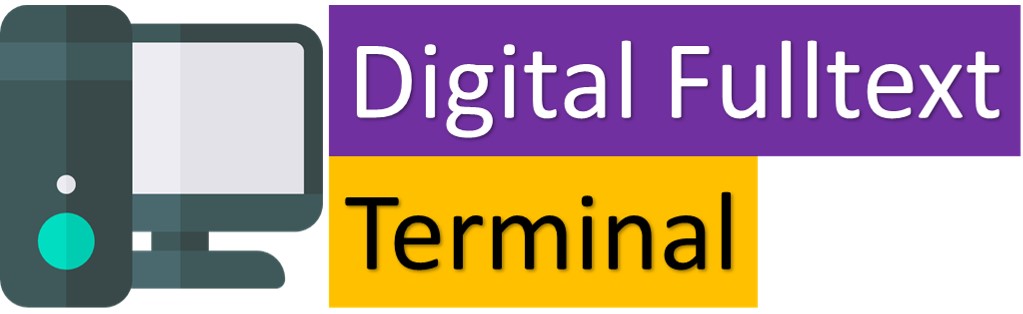
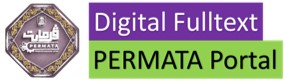
Physical Copy
ID Number
77964
Indexing
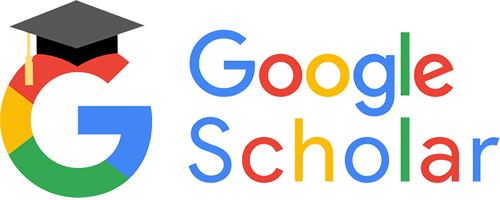
