Abstract
The main goal of this work presented in this thesis was to study the tribological properties of newly formulated semi-metallic friction material under different manufacturing parameters, material constituents and friction test parameters. In the first category, the optimization of manufacturing parameters (molding pressure, molding temperature and molding time) for producing the friction materials using powder metallurgy technique were investigated. The optimum manufacturing parameters were determined using Taguchi method where coefficient of friction (COF) and thickness loss were selected as the quality target. These optimal parameters were 500 kN molding pressure, 150°C molding temperature, and 600 seconds molding time. The results revealed that high molding pressure and temperature do not compulsorily produce the best performance in tribological properties. It could be explained by degradation of the resin structure and the loss of binding properties. The investigation also found that adequate molding time was required for sufficient binding of the tested materials. It was also observed that molding pressure has the strongest effect on physical and tribological properties. High molding pressure may cause the binder to separate from the brake friction material, thus less binder to hold the powder particles in the matrix. In the second category, a study was performed to investigate the effect of phenolic resin, rubber, calcium carbonate and graphite on the tribological properties. The samples were prepared under optimum manufacturing parameters. Samples with 15 wt.% of phenolic resin, 3 wt.% of graphite, 2 wt.% of rubber, 15 wt.% of calcium carbonate, 20 wt.% of steel fiber, 10 wt.% of ceramic fiber, 5wt.% of iron powder, 10 wt.% of copper chip, 8 wt.% of iron oxide, 8 wt.% of friction dust, 3 wt.% of magnesium oxide and 1 wt.% of barium sulphate were the optimum friction material formulation combination which shown the best tribological properties. Through this study, phenolic resin has the greatest influenced on the tribological properties of brake friction materials. Finally, the effect of applied loads and braking times on the tribological characteristics on indigenously formulated brake friction materials were also investigated using Chase dynamometer. Friction and wear tests were carried out under six different loads (445, 890, 1335, 1780, 2225 and 2670 N) and braking times (4, 8, 12, 16, 20 and 24 minutes) while the rotating velocity of the disc was kept constant at 500 rpm during the tests. The brake friction materials were examined for microstructural changes on worn surface using Scanning Electron Microscope (SEM). Generally, it was observed that COF decreases while wear volume increases with increasing of applied loads and braking times. The optimized friction material was observed to be suitable for temperature up to 250°C, load up to 1335 N and continuous braking time less than 20 minutes. An increase in wear volume was corresponding to the microstructural changes and the decomposition of organic materials. The severity of wear mechanism increases with an increasing of applied load and braking time. Test results show that the optimum selection of the manufacturing parameters and materials formulation have the most impact on the tribological and performance characteristics.
Metadata
Item Type: | Thesis (PhD) |
---|---|
Creators: | Creators Email / ID Num. Zaharudin, Aznifa Mahyam 2008349353 |
Contributors: | Contribution Name Email / ID Num. Thesis advisor Berhan, Mohamad Noor UNSPECIFIED |
Subjects: | T Technology > TA Engineering. Civil engineering > Materials of engineering and construction > Physical properties > Surface effects and tests T Technology > TJ Mechanical engineering and machinery > Machinery exclusive of prime movers |
Divisions: | Universiti Teknologi MARA, Shah Alam > Faculty of Mechanical Engineering |
Programme: | Doctor of Philosophy - EM990 |
Keywords: | Tribological properties, metallic friction, manufacturing parameters |
Date: | 2017 |
URI: | https://ir.uitm.edu.my/id/eprint/73696 |
Download
![[thumbnail of 73696.pdf]](https://ir.uitm.edu.my/style/images/fileicons/text.png)
73696.pdf
Download (167kB)
Digital Copy
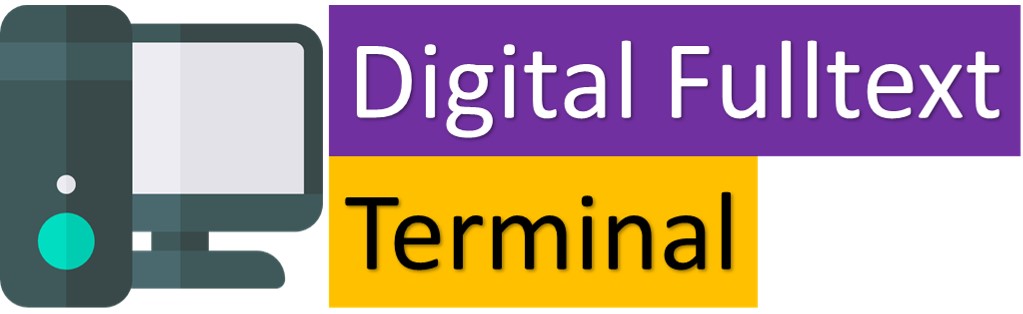
Physical Copy

ID Number
73696
Indexing
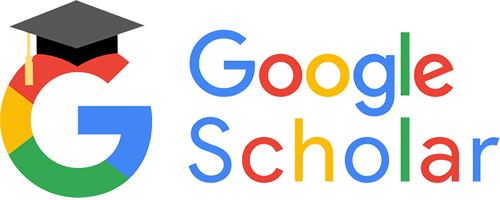
