Abstract
Owing to the increasing demands for eco-friendly epoxides derived from vegetable oils, much effort has been made regarding the epoxidation of palm oil in recent years. The oxirane rings are highly reactive to opening, especially through hydrolysis process to produced dihydroxystrearic acid (DHSA). At present, there are no studies on the production of DHSA using in situ hydrolysed epoxidized vegetable oil based on the optimum epoxidation process parameters. The aim of this study to produce in situ hydrolysed DHSA from optimum process parameters of epoxidized palm oil-derived oleic acid (EPOOA). EPOOA was produced by using in situ formed performic acid (PA). PA was formed by mixing formic acid (FA) as the oxygen carrier with hydrogen peroxide (HP) as the oxygen donor. The Taguchi method was used to optimize the epoxidation process for the maximum production of EPOOA. Then, in situ hydrolysis was used to produce DHSA from optimized EPOOA. The signal to noise (S/N) ratio analysis in Taguchi method showed that the optimum process parameters for production of EPOOA to the response of relative conversion to oxirane (RCO) with determination of oxirane oxygen content (OOC) was maximum (85.6%) under following conditions: (1) type of catalyst loading: sulphuric acid, (2) reaction temperature: 75°C, (3) stirring speed: 300 rpm, (4) FA/ oleic acid (OA) molar ratio: 1.0, and (5) HP/OA molar ratio: 1.5. The order of significance of the process parameters determined by analysis of variance (ANOVA) was as follows: catalyst type > stirring speed > HP/OA molar ratio > reaction temperature > FA/OA molar ratio. In addition, by using the optimized EPOOA, the effects of several process parameters (type of vegetable oil, oxidizing agents, catalyst concentration, HP concentration, type of process to produce the EPOOA, and hydrolysis method) on DHSA yield were studied. A mathematical model was developed by using the numerical integration Runge Kutta 4th Order method. In this model, the method was integrated with genetic algorithm optimization to determine the process model that fit with the experimental data using MATLAB software. After 100 iterations, the reaction rate constant based on optimized EPOOA for DHSA production were obtained as follows: fcn =0.841 mol-L^min1, k12 = 10.005 mol-L^-min-1, k2 = 0.099 mol-L^-min-1, and k3 = 0.011 mol-L^-min-1. Then, activation energy and thermodynamic analysis (enthalpy of activation, entropy of activation and free energy of activation) of DHSA production was identify based on Arrhenius equation. The results showed that there was good agreement between the simulation and experimental data, which validates the kinetic model. Overall, a high yield (80.7% with purity 98.50%) in situ hydrolysed DHSA was successfully produced from POOA by using optimum process parameters of epoxidation. IV
Metadata
Item Type: | Thesis (PhD) |
---|---|
Creators: | Creators Email / ID Num. Jalil, Mohd Jumain 2016306355 |
Contributors: | Contribution Name Email / ID Num. Thesis advisor Abdullah, Abdul Hadi (Assoc. Prof. Dr.) UNSPECIFIED |
Subjects: | T Technology > TP Chemical technology > Chemical engineering > Hydrolysis T Technology > TP Chemical technology > Biotechnology T Technology > TP Chemical technology > Food processing and manufacture |
Divisions: | Universiti Teknologi MARA, Shah Alam > Faculty of Chemical Engineering |
Programme: | Doctor of Philosophy (Chemical Engineering) - EH950 |
Keywords: | dihydroxystrearic, acid, DHSA |
Date: | March 2021 |
URI: | https://ir.uitm.edu.my/id/eprint/46589 |
Download
![[thumbnail of 46589.pdf]](https://ir.uitm.edu.my/style/images/fileicons/text.png)
46589.pdf
Download (163kB)
Digital Copy
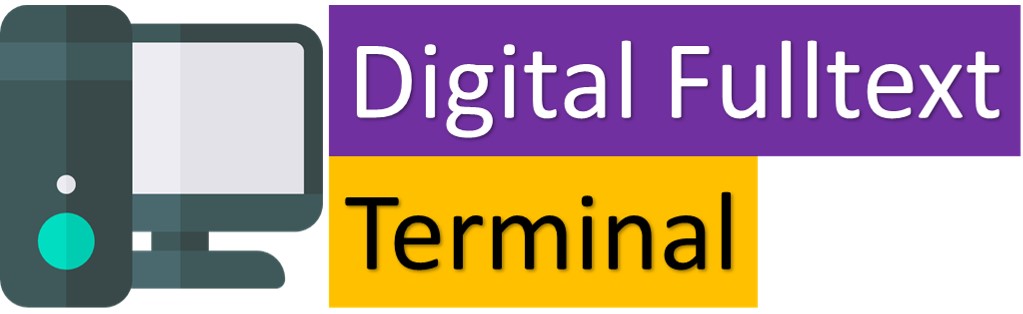
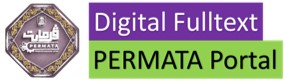
Physical Copy
ID Number
46589
Indexing
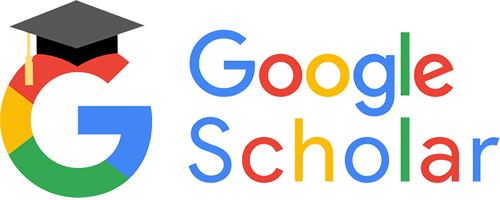
