Abstract
Reseach has been performed to develop a new binder that will allow powder metal injection moulding (MIM) of Molydenum High Speed Steel (M2 HSS). The development of the new binder parallels that of other binders utilised in MIM of other metal powder such as stainless steel, cemented carbides, tungsten heavy alloys, and cobalt based alloys. The binder/metal powder ratio, the mixing procedure, the injection moulding process, the debinding process and sintering process have been explored experimentally to optimise the MIM process using M2 HSS as the metal powder and waste rubber (WR) as one of the binder constituent
Injection moulding is a known and viable net-shape process for manufacturing small, complex shaped components, especially for high performance applications. Feedstock preparation for MIM is a vital step as shortcomings such as inhomogeneity of feedstock, metal particles segregation and metal powder-binder seperation cannot be corrected by subsequent processing adjusment. One key component in MIM is the selection of binder and the formulation as the binder promotes fluidity and rigidity of the feedstock particularly during mixing, injection moulding and debinding. The characterictics of the binder greatly affected MIM parameters such as particle packing, agglomeration, mixing, rheology, moulding, debinding, dimensional accuracy, defects and properties of the sintered MIM part Two binder systems have been successfully developed for MIM of M2 HSS components. The binder systems comprise of waste rubber binder combined with major fraction of conventional binder, paraffin wax and local binder based on palm oil derivative palm stearin. Paraffin wax (PW) and palm stearin (PS) can be removed rapidly by heptane leaching without deterioration of the green injection moulded parts. Polyproplene (PE) can be removed by prolysis during ramping up to the sintering temperature.
Studies have been performed to the feedstock compositions and to the process parameters in order to obtain high strength and dense components. Feedstocks having a powder loading of the 22um M2 HSS mixture up to 65 vol% can be injection moulded successfully. The developed binder systems provide flow ability of the M2 HSS particles and shape retention of the moulded parts. The brown parts were then sintered in vacuum atmosphere within a temperature range of 1200°C to 1260°C. Optimum sintered properties were obtained from the conventional binder, paraffin wax, whilst the sintered properties obtained from local binders palm stearin are comparable and good. The paraffin wax binder sintered at 1250°C possessed maximum density of was 8.095g/cm3 whilst palm stearin binder achieved optimum density of 8.111g/cm3 when sintered at 1240°C. The results suggested that the sintered density obtained from both binder systems have exceeded the theoretical density. The results also showed that optimum strength of paraffin wax and palm stearin binder were 2351Mpa and 2210MPa respectively, both recorded at sintering temperature of 1230°C. The strength of sintered parts for both binder systems decreases with increasing sintering temperatures which could be due to embrittlement of the part as a result of grain growth effect.
Metadata
Item Type: | Research Reports |
---|---|
Creators: | Creators Email / ID Num. Wahab, Nor ‘Aini UNSPECIFIED Omar, Mohd Afian UNSPECIFIED Ahmad, Ismail Nasiruddin UNSPECIFIED Nordin, Nor Amalina UNSPECIFIED Amir, Amalina UNSPECIFIED |
Subjects: | T Technology > TN Mining engineering. Metallurgy > Metallurgy > Powder metallurgy T Technology > TS Manufactures > Metal manufactures. Metalworking |
Divisions: | Universiti Teknologi MARA, Shah Alam > Research Management Centre (RMC) |
Keywords: | Powder metal injection moulding (MIM), Molydenum High Speed Steel (M2 HSS) |
Date: | 2014 |
URI: | https://ir.uitm.edu.my/id/eprint/13222 |
Download
![[thumbnail of 13222.pdf]](https://ir.uitm.edu.my/style/images/fileicons/text.png)
13222.pdf
Download (1MB)
Digital Copy
Physical Copy
ID Number
13222
Indexing
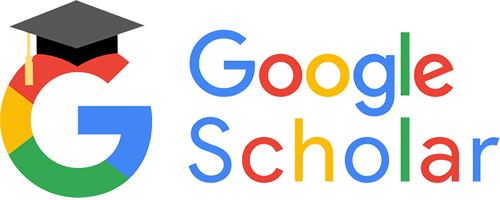
