Abstract
The primary challenge for manufacturers in the manufacturing industry is controlling process input parameters to achieve the desired surface roughness. A good pre-selection machining parameter is required to produce a high-quality surface. While a predictive model for surface roughness has generated significant interest, inadequate comprehension of the factors that influence surface roughness can result in insufficient pre-selection parameters, causing wastage of materials, time, and labour. The objective of this study is to use a simulation model to examine how variations in spindle speed impact the formation of tool edge trajectory pattern on a milled surface. The research employs a mathematical model to simulate the tool edge trajectory pattern of a two flutes end mill at various spindle speeds. This simulated end mill tool edge trajectory pattern represents the surface lay pattern formed on a milled surface during the end milling process when using a two flutes end mill. There are seven spindle speeds ranging from 1000rpm, 1500rpm, 2000rpm, 2500rpm, 3000rpm, 3500rpm, and4000rpm set for the simulation. The feed rate is fixed at 2000mm/min, the diameter ofthe tool is set at 12mm, and the tool path strategy is set for one way straight cutting path. Surface characterisation is achieved through a technique called watershed segmentation, which involves the segmentation of an image. In this study, the watershed segmentation method is utilised to identify and segment the tool edge trajectory pattern. The tool edge trajectory pattern produce diverse numbers and sizes of segmented areas for different spindle speeds. The trajectory pattern is quantified by segment area statistics, such as the number of segmented areas, the standard deviation of segmented areas, and the average size of segmented areas. The MATLAB R2017 programming software was selected to perform the simulation and the watershed segmentation process. A test was performed on a 5-axis universal CNC milling machine at varying spindle speeds, a constant feed rate, and a depth of cut of 0.2mm. The spindle speed, feed rate, and diameter of the end mill used in the experiment are the same as the parameters used in simulation. The surface texture were measured using the Alicona Infinite Focus Microscope (IFM). The surface texture was characterised using various parameters in accordance with ISO 25178, including the root mean square height (Sq),maximum surface height (Sz), developed interfacial area ratio (Sdr), auto-correlation length (Sal), and texture aspect ratio (Str). The analysis of the results indicated that boththe simulated and experimental tool edge trajectory patterns exhibited a continuous spiral shape in a forward motion. As the spindle speed increased, the number of loops in the pattern increased, leading to a rise in the number of segmented areas. However, the mean and standard deviation of the segmented areas decreased with increasing spindle speed because the size of the loops in the pattern became smaller, resulting in a smaller area being enclosed by the curves. Furthermore, an increase in spindle speed led to a decrease in surface roughness in the same way as the segmented area. Although parameters such as Sz, Sdr, and Str displayed different trends from the segmented areas, the values of Sq and Sal showed a similar decreasing trend with increasing spindle speed.
Metadata
Item Type: | Thesis (Masters) |
---|---|
Creators: | Creators Email / ID Num. Yusof, Fatiha Naziera UNSPECIFIED |
Contributors: | Contribution Name Email / ID Num. Thesis advisor Ismail, Mohd Fauzi (Ts. Dr.) UNSPECIFIED |
Subjects: | T Technology > T Technology (General) T Technology > TA Engineering. Civil engineering > Engineering mathematics. Engineering analysis > Mathematical models |
Divisions: | Universiti Teknologi MARA, Shah Alam > College of Engineering |
Programme: | Master of Science (Mechanical Engineering) |
Keywords: | Analysis, simulation, curves |
Date: | 2023 |
URI: | https://ir.uitm.edu.my/id/eprint/88661 |
Download
![[thumbnail of 88661.pdf]](https://ir.uitm.edu.my/style/images/fileicons/text.png)
88661.pdf
Download (16kB)
Digital Copy
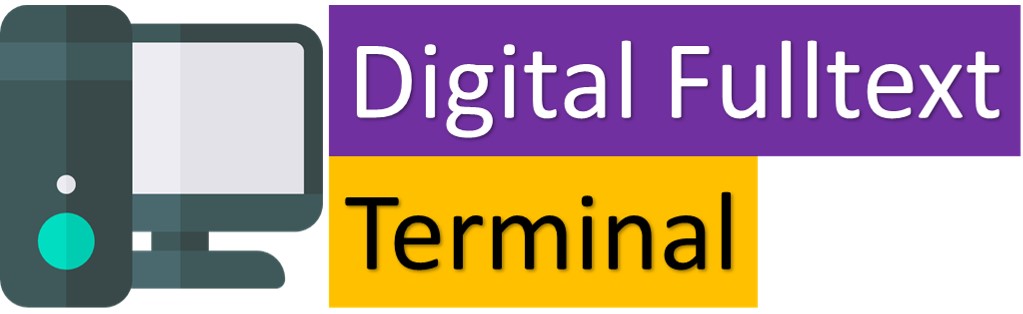
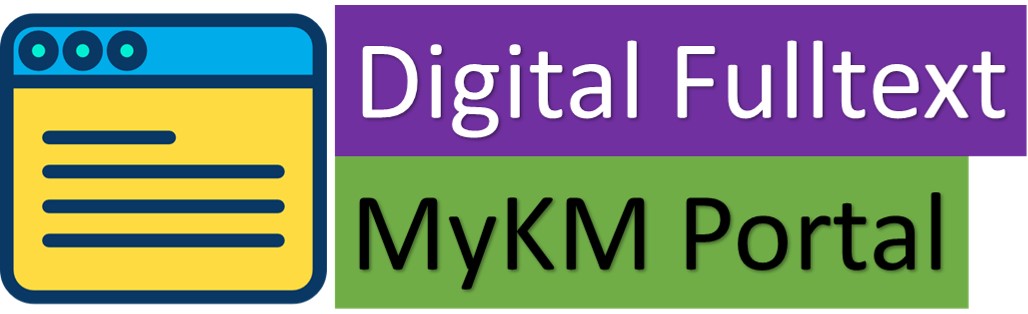
Physical Copy
ID Number
88661
Indexing
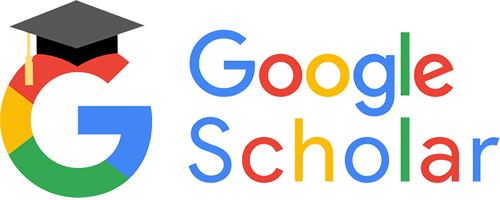
