Abstract
Bamboo is categorized as non-timber forest product and is a potential substitute for wood in wood based industry. Bamboo in its engineered form has received much attention and now is widely recognized as structural materials to replace wood in several applications. In Malaysia utilisation of indigenous tropical bamboo as veneer has not yet being explored. For this reason, Betong bamboo (Dendrocalamus asper) was chosen for making bamboo veneer due to its fast growth, large diameter, high flexural and renewability. Currently, the technology on producing bamboo veneer in Malaysia especially from local bamboos is not fully explored due to the lack of suitable peeler and technical know-how. Thus, this study explores the new potential of bamboo as veneer for the production of furniture components. Sesenduk (Endospermum diadenum) wood species were incorporated in the bamboo lamination to produce the hybrids so called the Hybrid Laminated Veneer Bamboo (HLVB). The production of HLVB has a high potential as material for interior design and furniture such as table top, chair seat, chair slat, arm rest and panelling to name a few. Sesenduk is pioneer under utilised species and its potential as substitute material for veneer is not yet being exploited. Apparently veneers are produced from wood with minimum diameter of 8 inches. In China, rotary peeling of bamboo to get veneers to make plyboard has been successfully produced. Realising their potential in China, a preliminary work on bamboo peeling was initiated at Timber Technology Centre, Forest Research Institute Malaysia FRIM Malaysia and results had showed that this technique can be applied to peel small diameter logs and branches of pioneer wood species in Malaysia (Anis, T, N et al 2013) provided that improvising and fabrication of this peeler machine is done. The novelty of using technique of rotary peeling is applied to produce veneer in this study. Currently, technique of slicing is used to produce Laminated Bamboo Veneer (LBV). This conventional technique is costly and tedious due to extra processing involved in converting bamboo sticks into larger dimension laminates. This involves the cost of gluing and jointing. Both flat and moulded furniture panels have been successfully produced for non-commercial use using veneers of this peeling technique (MTE, 2014). Applying the technique of bamboo peeling to small diameter logs realised the ‘waste to wealth approach whereby small diameter logs or branches is value added into interior design used. This approach is in line with the National Timber Industry Policy, NATIP (2009-2020) and related government policy to promote the utilisation of underutilised pioneer wood species like Sesenduk, Kelempayan, Ludai, Jelutong and Mahogany. In this study two types of board lamination were produced at different parameters. Lamination was done by flat platen press at 1500 psi and 2500 psi. Time and temperature of 20 minutes and 110 C were applied for both pressures. Urea formaldehyde was used as glue during pressing to ensure adhesion between veneer substrates. Two types of lamination namely Lamination 1 and Lamination 2 were produced; where both bamboo and sesenduk veneers were alternately laminated. Recovery, physical and mechanical properties were carried out. Results showed that the recovery rate is 50%, density for lamination 1 and Lamination 2 are 755 kg/m3 and 736 kg/m3 respectively. For Lamination 1, bending results showed MOE and MOR values of 4321 MPa (MOE) and
Metadata
Item Type: | Book Section |
---|---|
Creators: | Creators Email / ID Num. Ibrahim, Muhamad Iqram UNSPECIFIED Abdul Karim, Siti Rafedah UNSPECIFIED Mohamed, Suhaimi UNSPECIFIED Salleh, Hamid UNSPECIFIED Abdul Kadir, Yanti UNSPECIFIED |
Subjects: | T Technology > TS Manufactures > Furniture |
Divisions: | Universiti Teknologi MARA, Shah Alam > Research Management Centre (RMC) |
Event Title: | IIDEX 2014: invention, innovation & design exposition |
Event Dates: | 27 - 30 April 2014 |
Page Range: | p. 160 |
Keywords: | Bamboo veneer board; Furniture component; Furniture |
Date: | 2014 |
URI: | https://ir.uitm.edu.my/id/eprint/85378 |
Download
![[thumbnail of Research book: abstract only]](https://ir.uitm.edu.my/style/images/fileicons/text.png)
85378.pdf
Download (1MB)
ID Number
85378
Indexing
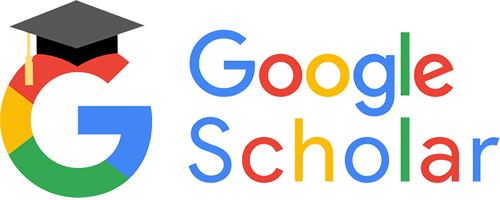
