Abstract
This report is a case study based on work carried out at Toshiba Capacitors (M) Sdn. Bhd., (TCM) an electronic manufacturer. TCM is considering improving the process yield and production efficiency of its existing manufacturing system. Three major phases of studies have been done in the production line and these include studying and analysing the existing conditions and problems of process flow and equipment layout. This study offers some proposals and guidelines on how to overcome these problems and is based primarily on the 4M factors. In addition, to perform problem solving in the process, throughout this study, we have introduced a SMEI PRO Theory as our approach in the evaluation. This theory is discussed in detail together with its application in the existing problems and conditions. The approach of this theory is based primarily on the sequential circling activities which should be implemented continuously. These activities are evaluation, improvement, standardisation and maintenance of the conditions. In order to maximise the effectiveness of the existing equipment throughout its entire life, improvement and maintenance activities should be accomplished continuously. It is to ensure a remarkable result is attained at all times.
Metadata
Item Type: | Student Project |
---|---|
Creators: | Creators Email / ID Num. Mohamad, Ahamad Yani UNSPECIFIED Hamzah, Ahmad Nazri UNSPECIFIED Basiran, Ishak UNSPECIFIED |
Contributors: | Contribution Name Email / ID Num. Thesis advisor Nathan, Padma UNSPECIFIED |
Subjects: | A General Works > Indexes (General) |
Divisions: | Universiti Teknologi MARA, Shah Alam > Faculty of Mechanical Engineering |
Programme: | Advanced Diploma in Mechanical Engineering |
Keywords: | Toshiba Capacitors (M) Sdn. Bhd., yield, production process |
Date: | 1995 |
URI: | https://ir.uitm.edu.my/id/eprint/75420 |
Download
![[thumbnail of 75420.pdf]](https://ir.uitm.edu.my/style/images/fileicons/text.png)
75420.pdf
Download (172kB)
Digital Copy
Physical Copy

ID Number
75420
Indexing
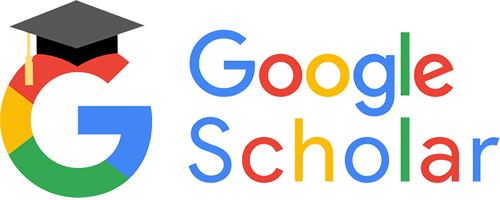
