Abstract
Modern day engineering structures depends on actively designing against fatigue failures. While Wire-Arc Additive Manufacturing (WAAM) offers numerous advantages to conventional manufacturing techniques, the fatigue performance of WAAM structures must be understood before they can be safely used. This thesis aims to investigate the relationship between the grain size microstructure of SS316L austenitic stainless steel and the mechanical properties of the WAAM component. The research is divided into four phases. The initial phase is the material verification and selection of the WAAM SS316L process parameters for thick wall structure using a Robotic welding system. The material chemical composition was verified by using an Arc spectrometer. The result was used for material modelling and computation. Included in this phase is the complex experimental thermal history data acquired by using a high-temperature thermocouple connected to a Data Acquisition System (DAQ) for thermal calibration. The second phase is the development of a Finite Element Method (FEM) WAAM model procedure using general-purpose numerical computational software MSC Marc/Mentat with utility routine and subroutine capability. Further, the temperature-dependent material parameter was developed in JMatPRO. The numerical computation is based on von Mises yield criterion and isotropic hardening rules. The numerical computational heat distribution in the WAAM model was calibrated by referring to the thermal experiment for verifying the heat transfer coefficients. As modelling a complex multi-pass welding simulation is a challenge due to the longer computational time, an innovative solution to simplify the Heat Source Model (HSM) was explored. As a result, a FEM procedure for WAAM model was developed. The third phase of the research is the analysis of SS316L material grain size microstructure and the grain growth material parameters at elevated temperature. A grain size prediction algorithm was developed specifically for SS316L material based on free grain growth formula. The real material parameters for the grain growth formula was investigated using a Dilatometer at elevated temperature with different holding times. At this stage, specific material parameters for the grain growth prediction subroutine was defined, such as activation energy (Q) and modified kinetic constant (Mo). In addition, an experimental investigation of the microstructure on the initial and final grain size according to ASTM guidelines was conducted. Evolution of grain sizes was observed within the as-printed WAAM structure. In the fourth phase, the mechanical properties of the as-printed WAAM component was defined. Differentiated by the upper and lower section, specimens for tensile, hardness and fatigue test were extracted from the experimental thick wall WAAM specimen. As a result, a novel FEM procedure for WAAM component was developed, calibrated and validated by experiment. Additionally, the grain growth material parameter for SS316L was defined as a temperature dependant material property and the grain growth behaviour was investigated. According to tensile, hardness and fatigue test standards, the mechanical properties and fatigue life of the WAAM component was defined for each section. A finer grain microstructure has an absolute effect of increasing the fatigue life of the WAAM component.
Metadata
Item Type: | Thesis (PhD) |
---|---|
Creators: | Creators Email / ID Num. Mat @ Muhammad, Muhd Faiz 2018668786 |
Contributors: | Contribution Name Email / ID Num. Thesis advisor HP Manurung, Ing Yupiter UNSPECIFIED |
Subjects: | T Technology > TS Manufactures > Metal manufactures. Metalworking |
Divisions: | Universiti Teknologi MARA, Shah Alam > College of Engineering |
Programme: | Doctor of Philosophy in Mechanical Engineering - EM950 |
Keywords: | WAAM, wire, mechanical |
Date: | 2022 |
URI: | https://ir.uitm.edu.my/id/eprint/72731 |
Download
![[thumbnail of 72731.pdf]](https://ir.uitm.edu.my/style/images/fileicons/text.png)
72731.pdf
Download (213kB)
Digital Copy
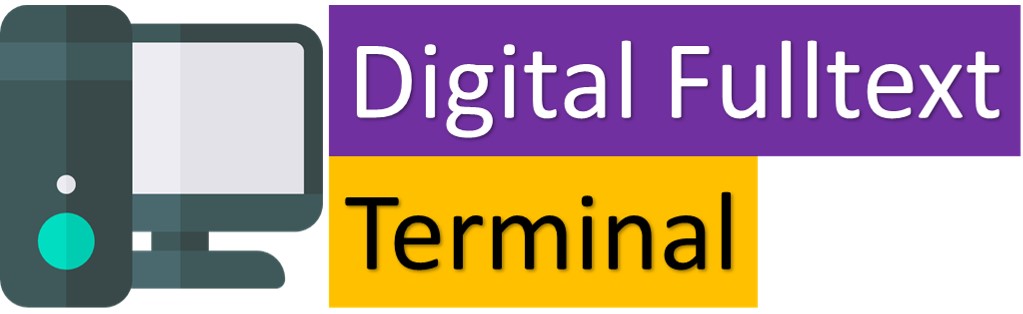
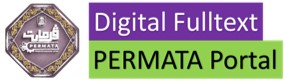
Physical Copy

ID Number
72731
Indexing
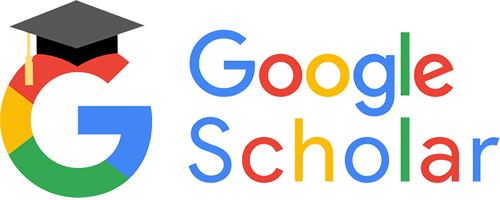
