Abstract
Base isolation is a technique installed to absorb any movement or vibration on the structures. Seismic base isolation causes the elongation of the fundamental period of vibration of the structure and hence it lowers the seismic demand. The incorporation of nanocomposites into elastomer as the interesting materials especially for the active stiffness and vibration control of structural systems. As a controllable stiffness element, nanocomposite elastomer can offer innovative engineering solutions to various engineering challenges. This research involves experimental work conducted at Engineering Design and Product Development (EDPD) unit of the Malaysian Rubber Board (MRB), Sungai Buloh, Selangor. This research’s aim is to study the performance of nanocomposites elastomer due to effect of nanocarbon and microcarbonyl iron fillers. The compounding process of elastomer was done using two roll mills and a conventional vulcanization system. The performances of material characterization of nanocomposite material were tested under tensile, hardness, rebound, dynamic mechanical, thermal, magnetic, and double shear. The microstructures of the nanocomposite material were observed using a Field Emission Scanning Electron Microscopy (FESEM). The fabrication and test of a down scale laminated elastomer was conducted to assess the performance of nanocomposite elastomer with different filler content due to shear and compression. It can be seen that nanocarbon with 1pphr experienced the highest 974.16% elongation at break. The overall hardness range for all samples are satisfied the requirements stated in BS ISO 48 (2018) is 35 to 85. It also shows that the highest strain value was obtained for the nanocomposite at 1 wt% of the nanocarbon. Morphology was affected by incorporation of filler, very high filler loadings showed poor dispersion of filler particles which was evidenced by the presence of agglomerates. This is clear that the dispersion of filler throughout the matrix was affected due to low filler-rubber interaction. From the shear and compression test, it shows that the incorporation of nanocarbon and microcarbonyl iron has a significant effect on the mechanical properties of the composites. By comparing the damping characteristics of the nanocomposite elastomer with conventional elastomer with damping ratio from 0% to 9% which falls into low damping rubber bearing category, it can be seen that nanocomposite elastomer with damping ratio from 13% to 24% and 16% to 25% respectively, belongs to high damping rubber bearing class. From these results, it can be concluded that the damping factor and storage modulus values evidenced that the degree of crosslinking was enhanced by addition of filler and improved further by altering an amount of filler. The specific applications of elastomer composite such as high performance mechanically was derived as the final outcome of this study. Perhaps these findings are significantly providing some valuable data.
Metadata
Item Type: | Thesis (PhD) |
---|---|
Creators: | Creators Email / ID Num. Ismail, Rozaina 2013291748 |
Contributors: | Contribution Name Email / ID Num. Thesis advisor Ibrahim, Azmi (Professor Dr.) UNSPECIFIED |
Subjects: | T Technology > TA Engineering. Civil engineering > Materials of engineering and construction > Nanostructured materials |
Divisions: | Universiti Teknologi MARA, Shah Alam > Faculty of Civil Engineering |
Programme: | Doctor of Philosophy (Civil Engineering) |
Keywords: | Base isolation system; elastomeric rubber bearing; nanofillers; rubber technology; nanocomposite elastomer; smart elastomer; magnetic |
Date: | October 2020 |
URI: | https://ir.uitm.edu.my/id/eprint/61023 |
Download
![[thumbnail of 61023.pdf]](https://ir.uitm.edu.my/style/images/fileicons/text.png)
61023.pdf
Download (36kB)
Digital Copy
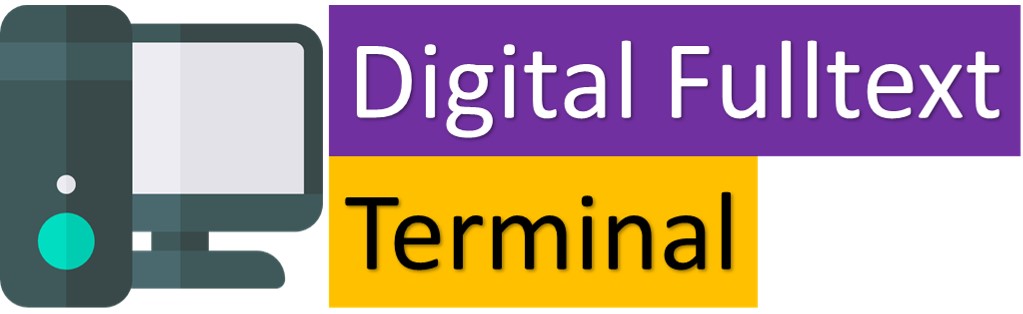
Physical Copy
ID Number
61023
Indexing
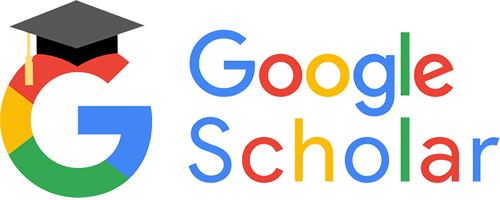
