Abstract
A low-velocity impact in composite structures could initiate a barely noticeable damage far from the surface. This undetectable damage could grow to a bigger size and could potentially lead to a catastrophic failure that might be resulting in a commercial waste or casualty. The ability of guided ultrasonic waves (GUW) to inspect the structures within a short inspection and quantify a complex damage scenario inside the structures are the golden goals in inspection method for composite structures. This study used a 3D model of an impact damage that represent a realistic impact damage and investigated the interaction of GUW with the impact damage using finite element method (FEM). The 3D FEM input model is prepared using MATLAB program codes. The input file is then exported to the Abaqus/Explicit software to run the simulation. The impact damage model is based on the experimental work, which is irregular in shape. There are four important investigation in this project: (1) investigating the accuracy of the impact damage model, (2) the influencing factors of wave scattering, (3) the interaction of wave scattering with multi-layered delamination and (4) the quantification method of the impact damage using GUW. From the first investigation, the model accuracy is verified and compared to the referred experimental works. Second study investigated the effects of different crack shapes, angular directivity, delamination depth and plate thickness on the wave scattering events. These influencing factors has caused significant changes on the amplitude intensity, especially on the past-defect location and within the damaged area. By investigating the effect of angular directivity on the wave scattering, it is obvious that the measurement performed not across the defective region will have no detection value, especially from the amplitude line scan. From the third study, which used the multi-layered delamination models, it can be observed that the increment in amplitude intensity are higher in the growing-size-delamination, compared to the same-size-delamination. This is closely related to the many changes in the delamination sides, area, width and length. The final study on the quantification method demonstrated that the line scan can provide a direct identification of the defect location and size. Meanwhile, the circular scan could estimate the defect size by looking at the opening of the side lobes. From the investigation on the individual monitoring points, the presence of the defect can only be detected by signals captured behind the damaged area, despite the location of the excitation point is changed to non-parallel position to the defect. This study concluded that the GUW is able to classify and characterize different defect parameters. The composite plates with and without defect have been modelled successfully using 3D FEM approach. The irregular-shaped combined defects (combination of delamination and 70% material degradation) has shown a good agreement with the experimental result, which could represent as a realistic impact damage. A library of information on defect detection has been formed, which will help for future works.
Metadata
Item Type: | Thesis (Masters) |
---|---|
Creators: | Creators Email / ID Num. Ibrahim, Noorfaten Asyikin 2016108545 |
Contributors: | Contribution Name Email / ID Num. Thesis advisor Murat, Bibi Intan Suraya (Dr.) UNSPECIFIED |
Subjects: | T Technology > TJ Mechanical engineering and machinery > Power resources |
Divisions: | Universiti Teknologi MARA, Shah Alam > Faculty of Mechanical Engineering |
Programme: | Master of Science (Mechanical Engineering) |
Keywords: | Low-velocity impact damage; guided ultrasonic waves; finite element modelling |
Date: | November 2020 |
URI: | https://ir.uitm.edu.my/id/eprint/59642 |
Download
![[thumbnail of 59642.pdf]](https://ir.uitm.edu.my/style/images/fileicons/text.png)
59642.pdf
Download (330kB)
Digital Copy
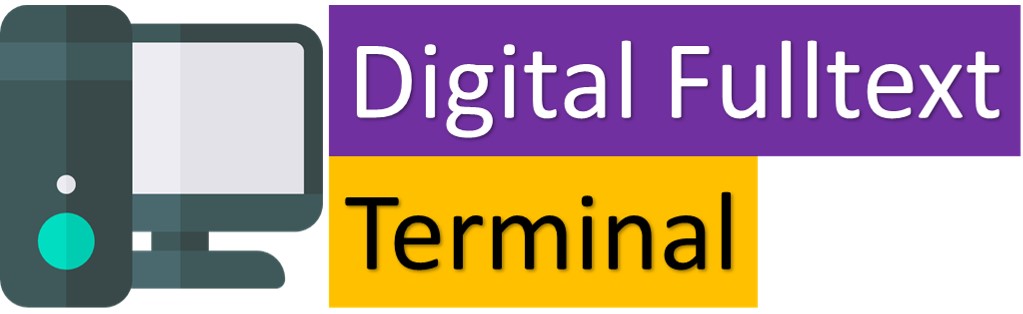
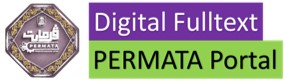
Physical Copy
ID Number
59642
Indexing
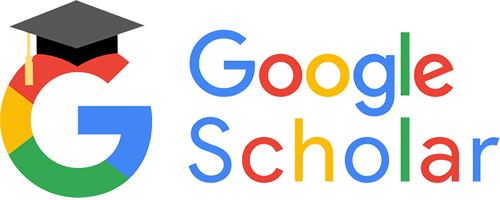
