Abstract
Nitrogen Oxide (NO) in stationary flue gas is a major cause of air pollution and its reduction is thus of great importance. Selective Catalytic Reduction (SCR), primarily using V2O5-WO3/TiO2 or V2O5-MoO3/TiO2 in the presence of ammonia, is a promising method for the removal of NO. Catalyst deposition, by means of a ceramic washcoat, which is primarily used in SCR, has been attributed to catalyst blockage and undesirable higher pressure drops. An alternative more efficient method is sought using dispersed V2O5 on Woven Stainless Steel Wire Mesh (WSSWM) multichannel monoliths. The WSSWM is initially coated with an alumina/silica (AI2O3- SiO2) mixture using the dip-slurry method. Impregnation of the catalyst is achieved using V2O5 precursor solutions of concentration 0.2, 0.4 and 0.6 M and calcination for 24, 48 and 72 hours at 500°C. Catalyst loadings varied between 2.63% and 50.58% w/w. The physical and chemical properties of the impregnated WSSWM monoliths were determined using TGA, XRD, N2 Adsorption, TPR and SEM-EDX. Results indicate that the catalyst is thermally stable up to 900°C and TPR profiles also indicate that there are three distinct reductions in NO concentration in the range 340-862°C. Surface analysis reveals that the catalyst surface morphology is heterogeneous irrespective of the precursor concentration and impregnation duration. The results from KH-Adhesion Testing for the prepared catalyst has excellent vibration resistance and is thus highly suited for flue gas application. NO reduction activity of m V2O5/ AI2O3- SiO2 (x) was performed on the in-house bench scale municipal solid waste incinerator (BS-MSWI) using cafeteria waste combustion to simulate NO emission. The % NO conversion was investigated according to flue gas temperature and excess air ratio at operating air flow rate of 100, 150 and 200 ℓ/min respectively. The optimum NO reductions of 82.1, 87.8 and 88.7% are achieved at 400°C and with an airflow rate of 200 L min-1 for precursor catalyst concentrations of 0.2, 0.4 and 0.6 M, respectively. The NO conversion effectiveness of developed catalyst of 88.7% is found to be comparable to that conventional SCR which shows that the NO conversion effectiveness is in the range of 90 - 92 %. MLR performed on the experimental data has enabled prediction of NO conversion over the studied range of independent variables and experimental conditions.
Metadata
Item Type: | Thesis (PhD) |
---|---|
Creators: | Creators Email / ID Num. Ismail, Kamariah Noor 2005489805 |
Contributors: | Contribution Name Email / ID Num. Thesis advisor Ku Hamid, Ku Halim (Prof. Dr.) UNSPECIFIED |
Subjects: | T Technology > TP Chemical technology > Chemical engineering T Technology > TP Chemical technology > Chemical engineering > Special processes and operations T Technology > TP Chemical technology > Industrial radiochemistry. Industrial radiation chemistry |
Divisions: | Universiti Teknologi MARA, Shah Alam > Faculty of Chemical Engineering |
Programme: | Doctor of Philosophy (Chemical Engineering) |
Keywords: | Catalyst, Solid waste, Combustion flue gas |
Date: | 2009 |
URI: | https://ir.uitm.edu.my/id/eprint/43394 |
Download
![[thumbnail of 43394.pdf]](https://ir.uitm.edu.my/style/images/fileicons/text.png)
43394.pdf
Download (175kB)
Digital Copy
Physical Copy
ID Number
43394
Indexing
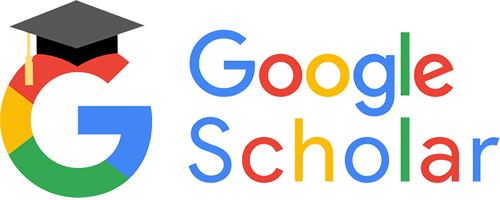
