Abstract
Agarwood is reputed to be most demanding and valuable wood in the world. Agarwood becomes an interest because of its usage such as in perfumery, medical and pharmaceutical purpose, incense and others. In extracting agarwood, hydro distillation is the most popular technique used in the industry. This technique is preferable due to factors of operational cost, safe to operate and environment friendly. There are several parameters that influencing the yield of the essential oil. One of them is temperature that be identified as the most influencing parameter in extracting the essential oil that effects the quality of the oil. Hence, this study is focused on the water temperature control of the agarwood extraction process. The water temperature exhibits nonlinear behaviour and the existence of advanced control like Model Predictive Control (MPC) is implemented to overcome this shortcoming. Previous studies have shown MPC has capability in handling the nonlinearity process better than conventional control technique. Generally, most of the extraction of agarwood is heated manually and took several hours or days to complete the whole process. Therefore, due to long extraction time, it will bring high energy consumption. Through the application of proper control technique, agarwood extraction process can produce better performance with low energy consumption. The performance has been evaluated based on transient response such as settling time, rise time and percentage of overshoot. In term of energy consumption, the evaluation is based on energy consumption index has been implemented. Three controllers namely PID control, Model Predictive Control (MPC) and self-tuning FuzzyPID are implemented in order to compare the transient response as well as energy consumption. First-Order-Plus-Dead-Time (FOPDT) model has been used to represent the system dynamic for the simulation studies. Real-time implementation has been carried out that based on the simulated controller. The evaluation on the performance and energy consumption of the proposed controllers were evaluated under simulation test and the findings showed MPC achieved better performance in term of transient response and improved in energy saving as compared to self-tuning FuzzyPID and PID control. The real-time application results indicated that MPC potentially managed to give good performance since it exhibited faster in rise time, settling time and produced small percentage of overshoot. In terms of energy usage, MPC significantly improved the energy consumption by 16.5 %, 18.7 % and 20 % as compared to PID control for step test, set point change test and load disturbance respectively.
Metadata
Item Type: | Thesis (PhD) |
---|---|
Creators: | Creators Email / ID Num. Mohammad, Nurul Nadia 2015480358 |
Contributors: | Contribution Name Email / ID Num. Thesis advisor Rahiman, Mohd Hezri Fazalul (PM Ts Dr) UNSPECIFIED |
Subjects: | T Technology > TK Electrical engineering. Electronics. Nuclear engineering > Dynamoelectric machinery and auxiliaries.Including generators, motors, transformers T Technology > TK Electrical engineering. Electronics. Nuclear engineering > Production of electricity by direct energy conversion |
Divisions: | Universiti Teknologi MARA, Shah Alam > Faculty of Electrical Engineering |
Programme: | Doctor of Philosophy |
Keywords: | Model Predictive Control (MPC), Agarwood, Wood |
Date: | 2019 |
URI: | https://ir.uitm.edu.my/id/eprint/40158 |
Download
![[thumbnail of 40158.pdf]](https://ir.uitm.edu.my/style/images/fileicons/text.png)
40158.pdf
Download (2MB)
Digital Copy
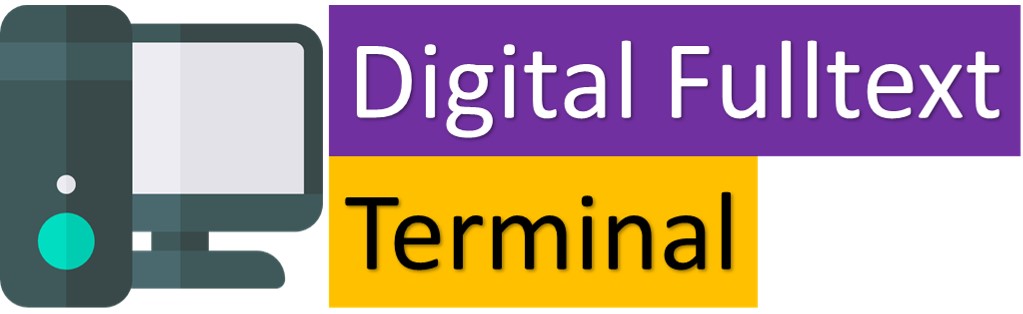
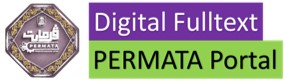
Physical Copy

ID Number
40158
Indexing
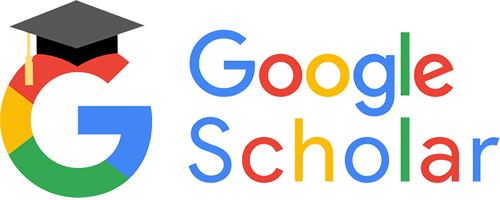
