Abstract
This study was undertaken to investigate physical, mechanical, morphological and thermal properties of polyester filled rubber toughened kenaf composite. The sample were exposed to four difference environments conditions. The condition were artificial sea water (sw), distilled water (ds), natural weathering exposure (exp) and soil buried (Soil). In this study, 25% weight of kenaf fiber were used in the composite. The filler size used in the range of 300-500um. Polyester resin was modified with 3 phr liquid natural rubber (LNR). The composite board was prepared by adding filler to modified polyester subsequently cross linked using methyl ethyl ketone peroxide (MEKP) and the accelerator cobalt octanoate 1%. The composite board were prepared by using compression moulding technique. The mechanical, chemical and morphology properties were investigated by using DMA, flexural , impact , FT-IR, SEM, hardness, fracture toughness and also water absorption test. All type of conditions exhibit a decrease in mechanical properties of composite with increasing time exposed. For flexural modulus and flexural strength, non- toughened composite in sea water immersion has better modulus of elasticity (MOR) and modulus of rupture (MOE) as compare with others condition. The decrement were only 11.52% for MOR and 10.25% for MOE. Non-toughened composite in distilled water immersion shows better impact properties than other condition with only 8% of decrement. Fracture toughness shows that toughened composite at natural weathering exposure had better result as compare with others condition with decrement were about 5.3%. The hardness value for all condition shows no significant value difference with the range between 80-85 shore D. Water absorption for all conditions increased with increasing of immersion time. There were no new peak observed from FTIR except for soil burial exposure. A new peak was observed at 3400 cm"1 - 3200 cm"1 . Morphological SEM showed the failure condition of composite mainly due to fibre fracture and fiber pull-out for all conditions. There is a gap between kenaf fibre and matrix for non- toughened composite and it has being observed by SEM. From DMA result, the addition of LNR had reduce Tg value around 16°C-21°C for all exposure condition. For long term used, the addition of LNR help to maintains composite strength and stability thus suitable used for marine applications. While the result was vice versa for natural weathering uses
Metadata
Item Type: | Thesis (Masters) |
---|---|
Creators: | Creators Email / ID Num. Shuhaimen, Nurul Shakirah 2011622886 |
Contributors: | Contribution Name Email / ID Num. Thesis advisor Bonnia, Noor Najmi UNSPECIFIED |
Subjects: | T Technology > TA Engineering. Civil engineering > Materials of engineering and construction > Composite materials. T Technology > TA Engineering. Civil engineering > Strains and stresses |
Divisions: | Universiti Teknologi MARA, Shah Alam > Faculty of Applied Sciences |
Programme: | Master of Science |
Keywords: | Polyester, mechanical, physcical |
Date: | 2017 |
URI: | https://ir.uitm.edu.my/id/eprint/37197 |
Download
![[thumbnail of 37197.pdf]](https://ir.uitm.edu.my/style/images/fileicons/text.png)
37197.pdf
Download (183kB)
Digital Copy
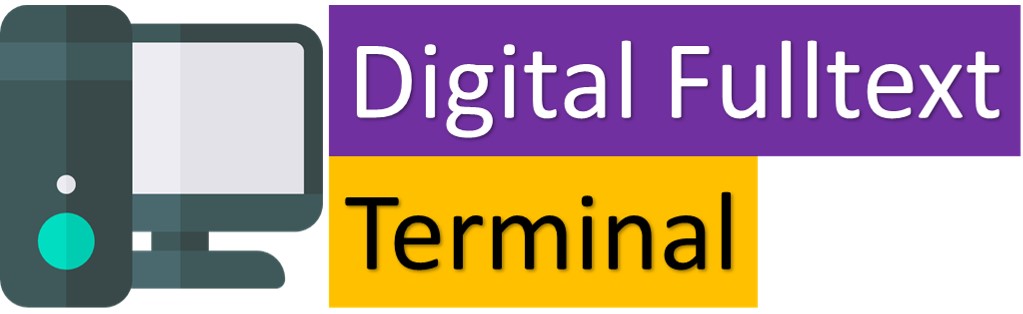
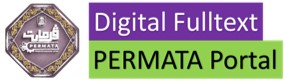
Physical Copy

ID Number
37197
Indexing
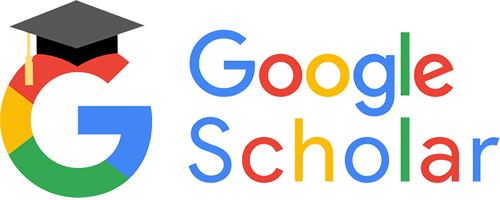
