Abstract
Wing box is an essential part of an aircraft. The wing box includes the structural members of the wing such as spars, ribs, braces, bars, struts etc. and is enclosed by the upper and lower skins of the wing. Generally the roots of the front and the rear spars are connected to the fuselage. The spars typically resist the bending and twisting loads and the shearing loads are taken on by the skin. The assembly of the structure may include the use of nonmetallic composite components and the bonding of metal structures as well as the use of conventional metal alloys and fasteners. So it's critical for engineer to do research and testing of the structure before full wing is being constructed. To do such test, engineers need a reliable device to examine the strength and the ability of the wing box. In the wing box testing, structural frame will be exposed to high force applied onto it. A test rig concept to investigate the technology is developed in detail using a systems engineering design process. Suitable design and several analyses will be done through the correlation formulation or related calculation theory with this part. Structure involved in this particular exercise should have greater strength to withstand force applied. Having proper joining method is essential to ensure structure stability and reliability. Joining process method should be carefully analyzed to ensure structure can withstand much greater force than the wing being tested.
Metadata
Item Type: | Thesis (Degree) |
---|---|
Creators: | Creators Email / ID Num. Zulkefley, Mohd Safwan 2005753929 |
Contributors: | Contribution Name Email / ID Num. Thesis advisor Ramly, Ramzyzan UNSPECIFIED |
Subjects: | T Technology > TA Engineering. Civil engineering > Materials of engineering and construction |
Divisions: | Universiti Teknologi MARA, Shah Alam > Faculty of Mechanical Engineering |
Programme: | Bachelor Engineering (Hons) (Mechanical) |
Keywords: | Wing box, Design, Frame |
Date: | 2009 |
URI: | https://ir.uitm.edu.my/id/eprint/36779 |
Download
![[thumbnail of 36779.pdf]](https://ir.uitm.edu.my/style/images/fileicons/text.png)
36779.pdf
Download (4MB)
Digital Copy
Physical Copy

ID Number
36779
Indexing
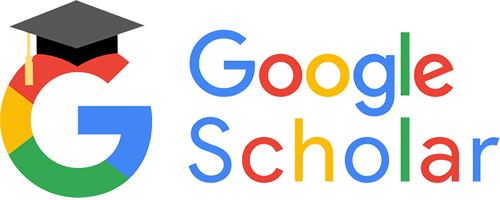
