Abstract
The energy consumption in machining process nowadays is extremely high which lead to significant impact on many aspects especially on manufacturing industry and environment.There are lot of study discussing about how to save energy on the manufacturing industries.In this project milling process parameter have been investigated for minimizing the consumption of energy via experimental approach where the power consumption was recorded by the clamp multi Fluke 345 PQ Clamp Meter while mildsteel (AISI 1018) being cut using conventional milling machine. The cutting tool High Speed Steel(HSS) was used in the experiment. The process parameters that involved was spindle speed (RPM), feed rate (m/min), and depth of
cut (mm). By using response surface method(RSM) the result of the experiment have been evaluated and analyzed and obtain the optimized process parameters to minimize
the consumption of energy where the spindle speed is 220 rpm,feed rate is 0.218 m/min and depth of cut is 0.1mm.The rsm also generate interaction equation between
parameters with the accuracy of 94.39% from the experimental data.At the end of the study,feed rate is the most influential milling parameters that affect to energy
consumption.From the result it concluded that higher feed rate decrease machining time which lead to lower energy consumption.
Metadata
Item Type: | Student Project |
---|---|
Creators: | Creators Email / ID Num. Zakaria, Muhammad Zahizan 2013442082 |
Subjects: | T Technology > TJ Mechanical engineering and machinery > Energy consumption T Technology > TJ Mechanical engineering and machinery > Energy conservation |
Divisions: | Universiti Teknologi MARA, Pulau Pinang > Permatang Pauh Campus > Faculty of Mechanical Engineering |
Programme: | Bachelor of Mechanical Engineering (Manufacturing) (Hons.) |
Keywords: | manufacturing industry,environment,High Speed Steel |
Date: | 2017 |
URI: | https://ir.uitm.edu.my/id/eprint/30586 |
Download
![[thumbnail of 30586.pdf]](https://ir.uitm.edu.my/style/images/fileicons/text.png)
30586.pdf
Download (149kB)
Digital Copy
Physical Copy

ID Number
30586
Indexing
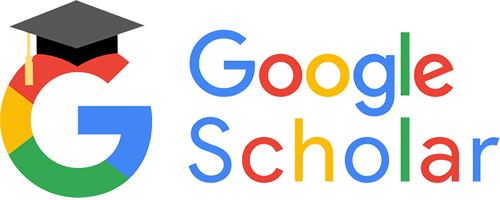
