Abstract
One of the premature failures of truck and bus tyres is associated with temperature rise known as blowout that occurs in the thick shoulder regions of the tyre. It occurs due to various dissipative processes under dynamic deformations. The heat produced is sufficiently high to cause thermal degradation that produces volatiles, which consequently exerts internal pressure sufficiently large to tear open a path to the exterior. Blowout failure may cause fatal road accidents. Although the tyre industry is aware of the problem, research in this area is still inadequate apart from the work conducted by Gent and Hindi in 1988, Choi and Kim in 1998 and Park in 2000. The factors affecting heat generation are still not fully investigated, thus the work presented in this thesis has covered the areas which are not covered by the previous researchers. This includes the work to investigate the effects of glass-transition temperature, Tg of the rubber, partcicle size of the filler, structure of filler, viscosity of process oil and coupling agent on silica-filled vulcanizate on temperature rise and blowout failure. Temperature rise and blowout failure tests were conducted by subjecting a cylindrical test-piece to flexing in a compression flexometer at a constant displacement amplitude in accord with IS0466/3-1982. The compression flexometer was modified accordingly to monitor the temperature rise in the interior of the test-piece continuously until the occurrence of blowout failure. Thus this enables the true blowout temperature to be registered. Some of the interesting findings are highlighted in this abstract. In unfilled vulcanized rubber, the temperature rise was found to increase in the increasing order of the Tg of the rubber, NBR>SBR>NR. However, the heat produced was not sufficiently high to cause blowout failure because the heat generated by mechanical work was not sufficiently high either to cause degradation of rubber or to cause breaking of chemical crosslink. In black-filled vulcanizates, temperature rise and blowout were affected by the Tg of the rubber, filler loading, particle size and filler structure. Increasing the Tg, filler loading, filler structure and decreasing the particle size increased temperature rise and shortened the blowout time. The blowout failure was also affected by the process oil. Blowout time was shorter with paraffinic oil than aromatic oil. In the case of silica-filled vulcanized rubber, temperature rise and blowout temperature increased with increasing amount of coupling agent (TESPT) beacuse the hardness increased progressively with increasing TESPT and hence higher dynamic work was required to deform the test-piece at a constant displacement amplitude. The results show that the actual blowout temperature was much higher than the temperature recorded at the base of the test-piece. The blowout temperature of the interior of the test-piece was 200°C for NR and 230 - 240°C for NBR and SBR respectively. These actual blowout temperatures are in good agreement with those reported independently by Gent and Hindi, and that of Choi and Kim.
Metadata
Item Type: | Thesis (PhD) |
---|---|
Creators: | Creators Email / ID Num. Said, Che Mohamad Som 2003868200 |
Contributors: | Contribution Name Email / ID Num. Thesis advisor Samsuri, Azemi UNSPECIFIED |
Subjects: | Q Science > QC Physics > Heat T Technology > TA Engineering. Civil engineering > Materials of engineering and construction > Plastics |
Divisions: | Universiti Teknologi MARA, Shah Alam > Faculty of Applied Sciences |
Programme: | Doctor of Philosophy |
Keywords: | Thick rubber, vulcanizates, blowout |
Date: | 2014 |
URI: | https://ir.uitm.edu.my/id/eprint/16406 |
Download
![[thumbnail of 16406.pdf]](https://ir.uitm.edu.my/style/images/fileicons/text.png)
16406.pdf
Download (166kB)
Digital Copy
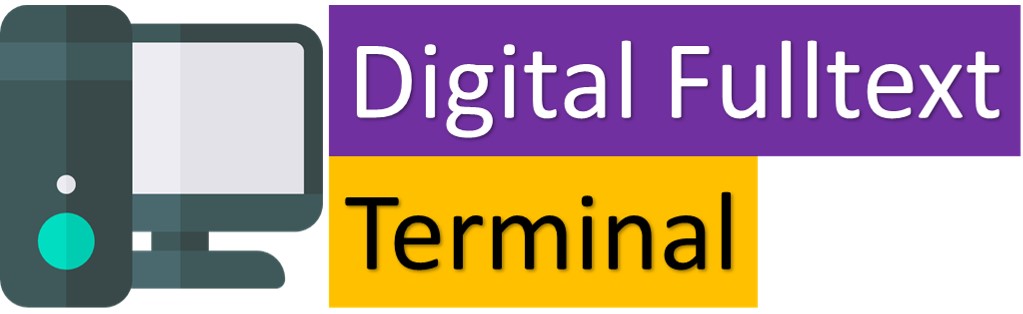
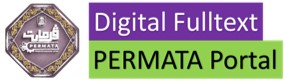
Physical Copy

ID Number
16406
Indexing
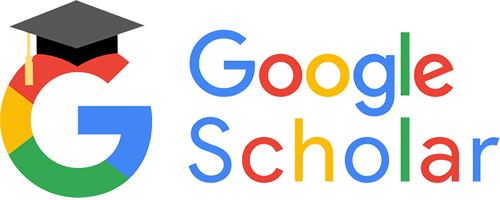
