Abstract
Heat transfer contributed in almost all processes in process industry. In contrast, mass transfer or chemical reaction can be dominant in some processes, while negligible importance in other processes. This major role of heat transfer underlines the importance of devices which function is to transfer heat into and out of a process. This device is a heat exchanger. Heat exchangers are used to transfer heat between two or more fluids, or between fluid and solid, which have opposite temperature to each other. Shell-and-tube heat exchangers (STHEs) are the most common types o f heat exchangers, covered about 60% of all heat exchangers used. Temperature process systems especially Shell-and-Tube Heat Exchanger (STHE) have nonlinear characteristic which exhibit oscillatory and long dead-time behavior. Conventional P1D controller usually used for slow process such as temperature but having poor control in some specific process.. Therefore, the main objective of this research is to design and control a new hybrid model reference adaptive fuzzy logic controller (MRAFLC) for temperature control problems in STHE system. In addition, the performances of this new design will be evaluated using certain performance criterion and these performances will be compared to the conventional PID controller and Fuzzy Logic Controller (FLC). The designs of MRAFLC consist of two parts which are the FLC part and the model reference part. The design of FLC part consists o f the design of membership function (MF), design of rule bases and design of Fuzzy Inference Structure (FIS). The combination of FLC part and model reference using Gaussian MF and 7x7 rule bases for both parts has been chosen as the best MRAFLC designs. The MRAFLC performances have been evaluated during six different set point tests and two different load disturbances tests. These performances have been comparing with PID controller and FLC. The MRAFLC responses exhibit the lowest MO/MU for all set point tests ranging from no MO/MU until 35.25% MO/MU. In addition, MRAFLC responses have the most reduced cycles or oscillations as the minimum is zero cycle while the maximum is one cycle. An improved MRAFLC structure has been design to improve the MRAFLC design during set point test from 39°C to 35 and 43°C to 35°C in order to have a MU within a desirable limit, which is below 20%. This improved MRAFLC has lowered the MU to 12.46% and 10.08% respectively. For load disturbances tests, MRAFLC exhibits the lowest decay ratio during 10% and 20% load ranging from zero decay ratios to 13.45% as PID controller produce the highest decay ratio during both tests. The performances of MRAFLC has significantly importance during step down of 20% load as it produce below 25% of decay ratio whereas both PID controller and FLC exhibit response above 25%, which is not desirable for a temperature control loop. In addition, MRAFLC produces shortest response time, lowest overshoot and less oscillation with one cycle when subjected to noise disturbances. All the findings indicate that the new design of MRAFLC not only improved the performance of conventional PID controller and FLC, but more importantly its performances are within a desirable limit for set point temperature change tests, load and noise disturbances tests.
Metadata
Item Type: | Thesis (Masters) |
---|---|
Creators: | Creators Email / ID Num. Ahmad, Mohd Aizad 2010671546 |
Contributors: | Contribution Name Email / ID Num. Thesis advisor Ishak, Abdul Aziz UNSPECIFIED Thesis advisor Noor Ismail, Kamariah (Dr) UNSPECIFIED |
Subjects: | Q Science > QD Chemistry > Organic chemistry > Polymers. Macromolecules |
Divisions: | Universiti Teknologi MARA, Shah Alam > Faculty of Chemical Engineering |
Programme: | Master of Science |
Keywords: | Heat transfer; Process industry; Temperature process systems |
Date: | May 2013 |
URI: | https://ir.uitm.edu.my/id/eprint/16295 |
Download
![[thumbnail of TM_MOHD AIZAD AHMAD EH 13_5.pdf]](https://ir.uitm.edu.my/style/images/fileicons/text.png)
TM_MOHD AIZAD AHMAD EH 13_5.pdf
Download (1MB)
Digital Copy
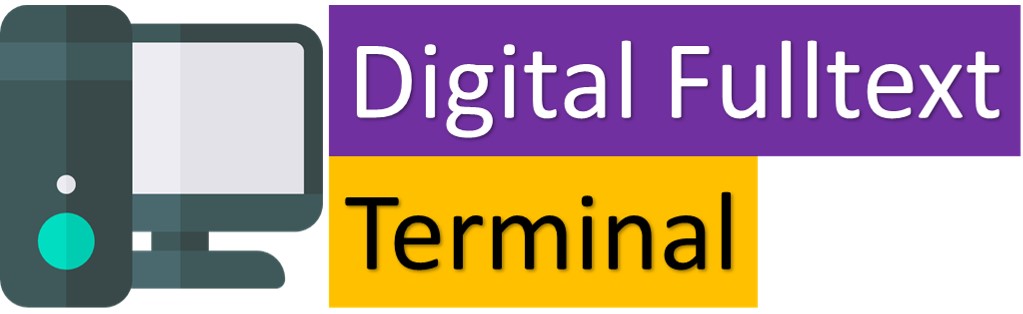
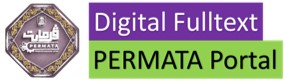
Physical Copy
ID Number
16295
Indexing
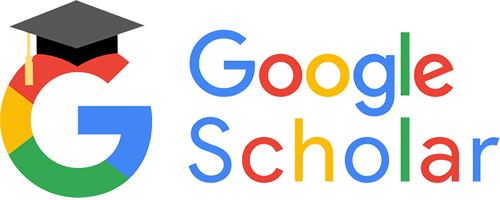
