Abstract
This thesis presents an integrated investigation of various aspects of hydrodynamic lubrication in a journal bearing. Hydrodynamic journal bearings arc critical power transmission components used to carry high loads in different machines applications. In machine design, it is essential to know the true or expected operating conditions of the bearings. These operating conditions can be explored in laboratory using a specific test rig. In the present study, the hydrodynamics lubrication behaviour in a journal bearing has been investigated. The work described is based on the direct measurement of temperature, pressure, frictional force and ultrasonic reflection coefficients from a fluid interface using longitudinal and shear transducers. Measurement of temperature profile in hydrodynamic lubrication journal bearing has been investigated for different conditions later compared to predicted values from effective temperatures. In this study effective temperatures were calculated by two different methods using (1) Raimondi and Boyd chart s and (2) inlet and outlet temperature values. From the results obtained, it was found that speed, load, oil inlet supply pressure and oil groove locations have affected the temperature profiles to some extent. In other investigation, measurements of pressure profiles in hydrodynamic lubrication in journal bearing were plotted. Predicted maximum pressure from Raimondi and Boyd charts were obtained for comparison purposes. Theoretical pressure profiles by short-bearing and long-bearing approximations were computed. It was found that the experimental maximum pressure is higher compared to the predicted value. In another investigation, an ultrasonic method was deployed to map thickness profile around the journal bearing. A purpose built transducer using a longitudinal wave was used to obtain the reflection coefficient from the lubricant layer. The thickness profile obtained in converging section agrees well with classical hydrodynamic predictions. In the diverging section, transformation from reflection coefficient values to oil film thickness is no longer valid due to the presence of a second phase, air. This caused the reflection coefficient values tend to 1. In measurement of viscosity around bearing circumferential, a shear wave was deployed to obtained reflection coefficient from the lubricant layer. A different plug was used for the purpose built transducer. Viscosity values were calculated using Spring Model for thin layer and Bulk Model in thick layer. It was observed that viscosity in operating journal bearing differ from the values obtained by effective temperatures.
Metadata
Item Type: | Thesis (PhD) |
---|---|
Creators: | Creators Email / ID Num. Ahmad, Mohamad Ali UNSPECIFIED |
Subjects: | T Technology > TJ Mechanical engineering and machinery > Machinery exclusive of prime movers > Tribology. Lubrication and friction > Lubricants |
Divisions: | Universiti Teknologi MARA, Shah Alam > Faculty of Mechanical Engineering |
Programme: | Doctor of Philosophy |
Keywords: | Lubrication |
Date: | December 2014 |
URI: | https://ir.uitm.edu.my/id/eprint/16200 |
Download
![[thumbnail of 16200.pdf]](https://ir.uitm.edu.my/style/images/fileicons/text.png)
16200.pdf
Download (1MB)
Digital Copy
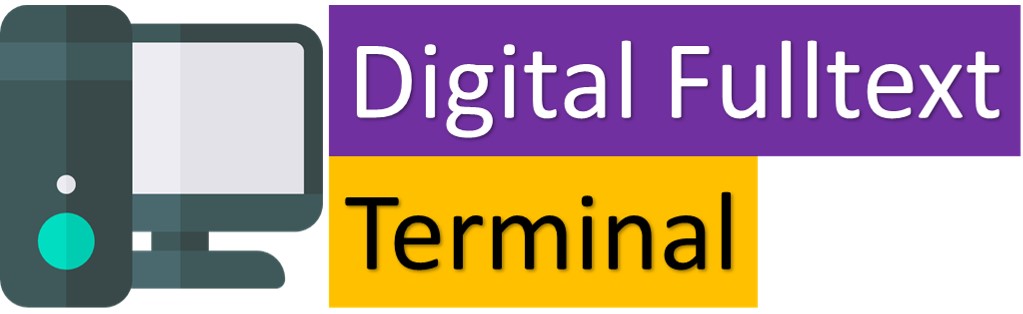
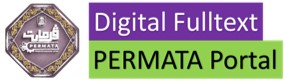
Physical Copy
ID Number
16200
Indexing
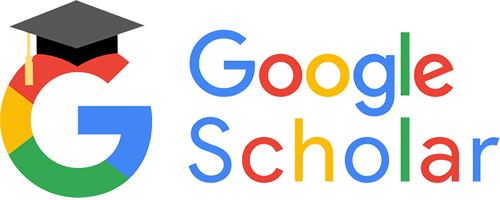
