Abstract
Lumbar spinal fusion or lumbar interbody fusion is a surgical procedure done by putting the cages implant between the lumbar vertebra supported by rods and screws to hold the vertebra, widely accepted as one of the surgical procedure to treat disc degeneration diseases and other medical conditions. However, vertebral endplate subsidence failure has been detected as one of the major problems that might increase the potential of pain and mechanical instability. The many designs and material type of the spinal implants of cages that can be used in spinal fusion should be carefully considered. Posterior lumbar interbody fusion (PLIF) cage is used in the procedure to maintain stability and promote fusion between vertebrae. There are four different types of biomaterials the cage can be made up of. They are metal, ceramic, polymer and composite. The Posterior Instrument (PI) such as the pedicle screw and rod are made by Titanium Alloy. The purpose of this study is to examine the interbody fusion effect of a different type of material group such as metal and composite cage for use in lumbar fusion. 3D vertebrae model (L3-L4) with interbody fusion use different material properties such as PEEK, PLA, Cobalt Chromium, Titanium Alloy and Stainless Steel. A finite element model of the lumbar vertebrae was used. A fusion model with pedicle screw systems implanted at the L3–L4 levels were developed based on the respective surgical protocols. The Von Mises stress and displacement of the cage at the vertebra were measured under different compressive loading conditions and motion. Subject comparison showed a significant effect of material properties on flexibility in extension, axial rotation and lateral bending but not in flexion. Titanium Alloy is a good material for the metal categories for the cage and PI, and from composite categories is PLA (Polylactic acid) that can be an alternative material which would provide cheaper material and lower production cost. The cage subsidence occurred at both materials, with an overall of higher cage-endplate stresses for stainless steel, in comparison to PLA and controlled configurations. In addition, the stress distribution in PLA cage are better. Further investigation of PLA cage’s mechanical properties should be done to determine the accuracy and reliability of the simulation.
Metadata
Item Type: | Thesis (Masters) |
---|---|
Creators: | Creators Email / ID Num. Yahya, Rusnani UNSPECIFIED |
Contributors: | Contribution Name Email / ID Num. Thesis advisor Abdullah, Abdul Halim UNSPECIFIED |
Divisions: | Universiti Teknologi MARA, Shah Alam > Faculty of Mechanical Engineering |
Programme: | Master of Science in Mechanical Engineering |
Keywords: | Material, Properties, Cage |
Date: | 2019 |
URI: | https://ir.uitm.edu.my/id/eprint/87945 |
Download
![[thumbnail of 87945.pdf]](https://ir.uitm.edu.my/style/images/fileicons/text.png)
87945.pdf
Download (156kB)
Digital Copy
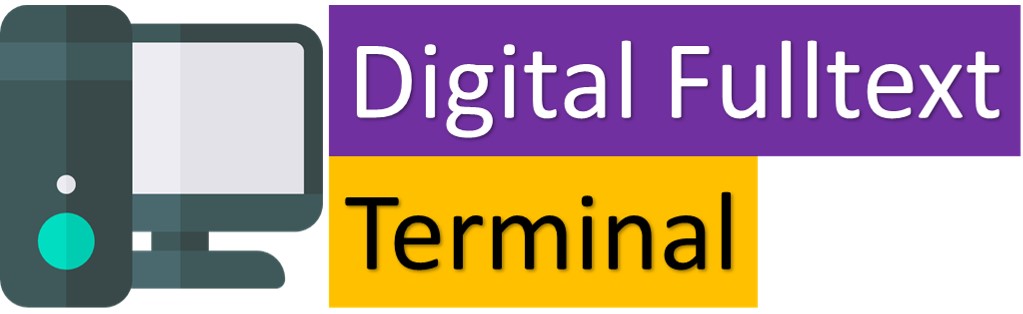
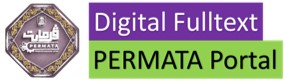
Physical Copy
ID Number
87945
Indexing
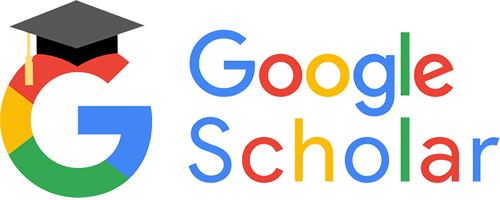
