Abstract
Deformation of distinct layup of Hybrid Composites Carbon and Glass Fibre Reinforced Polymer(C/GFRP) unidirectional, off-axis shear dominated, balanced crossply and quasi isotropic under tensile, flexural and shear loading composite are subjected to debate. This study establishes comprehensive procedures of characterization and failure prediction of hybrid C/GFRP structural laminates based on the properties of CFRP and GFRP before utilized in structural design. It also established multi methods in mechanical properties extraction of Hybrid Composite C/GFRP using Laser Vibrometer, Strain Gauge, Digital Image Correlation (DIC) and Multi scale Finite Element Modelling. Novel positioning chart of Unidirectional, Off- Axis Shear Dominated, Quasi Isotropic and Balanced Cross Ply C/GFRP with respect to Tensile Strength and Flexural Strength, Tensile Modulus and Flexural Modulus, Strain to Failure (Tensile and Flexural), for composite design selection has been developed. The findings from tensile test on hybrid composite C/GFRP Symmetrical UD, Symmetrical Cross Ply, Quasi Isotropic shows that Modulus of Elasticity locates in between CFRP and GFRP respectively but Tensile Strength rely significantly on the delamination between C/GFRP layers i.e. interlayer delamination as major failure mode along with other combined failure modes such as intra layer delamination on carbon fiber, matrix cracking and propagation, fiber bridging, fiber kinking and fiber rupture. Strain to failure is observed to improve for unidirectional, cross ply and quasi isotropic hybrid composite under tensile loading due to effect of hybridization and presence of GFRP layups. 10º off-axis tensile test has been performed on hybrid composites C/GFRP and exhibits the trend of incremental Shear Modulus, G12 proportionately with respect to number of GFRP layers in hybrid composites C/GFRP. Hybrid composites with highest thickness of GFRP recorded the highest shear modulus due to increased occurrence of ductility of matrix and better interfacial bonding. Three point bending test has been performed on hybrid composites and observed that there is improvement of flexural strength, enhanced flexural modulus as compared to constituent GFRP and higher flexural strain to failure compared to constituent CFRP due to higher elongation capability of GFRP. It can be concluded that the tensile properties are mainly influenced by the strength and stiffness of the carbon fiber. The significant increase in flexural strength observed in hybrid composite C/GFRP has been attributed to the optimum harnessing of the compressive potential of the glass fiber during placement at the location of maximum compressive stress. The study on full field deformation using digital image correlation technique on both tensile and flexural found that deviation of median value of strain depends on the hybridization of C/GFRP where higher content of CFRP reduces the variation of strain computed from DIC in comparison with FEM. Finite element based failure prediction using maximum stress criteria on tensile test shows close agreement with experimental values but varies significantly for all other layup cases. It is due to limitation of FEM capability which does not incorporate failure mechanism such as matrix cracking, fiber rupture i.e. damage propagation. The study provides new insight on the deformation behaviour of hybrid composites under different mode of loading; tensile, shear and bending. It also offers good understanding on how variability in the carbon /glass fibre orientation can influence hybrid effects in composite laminates.
Metadata
Item Type: | Thesis (PhD) |
---|---|
Creators: | Creators Email / ID Num. Ab Ghani, Ahmad Fuad 2015412806 |
Contributors: | Contribution Name Email / ID Num. Thesis advisor Mahmud, Jamaluddin UNSPECIFIED |
Divisions: | Universiti Teknologi MARA, Shah Alam > Faculty of Mechanical Engineering |
Programme: | Doctor of Philosophy (Mechanical Engineering) – EM950 |
Keywords: | Glass Fibre Reinforced Polymer, hybrid, C/GFRP |
Date: | 2019 |
URI: | https://ir.uitm.edu.my/id/eprint/83851 |
Download
![[thumbnail of 83851.pdf]](https://ir.uitm.edu.my/style/images/fileicons/text.png)
83851.pdf
Download (101kB)
Digital Copy
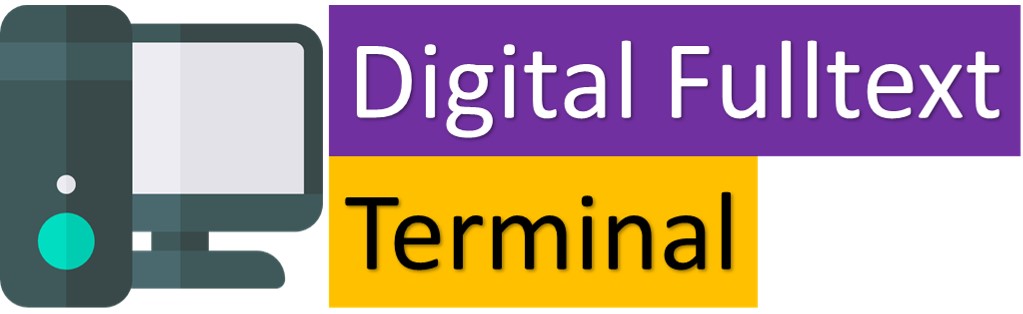
Physical Copy
ID Number
83851
Indexing
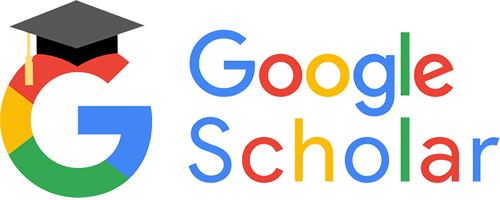
