Abstract
Aluminium alloy swarf (AAS) is by-product obtained from the automotive manufacturing industry. It is conditioned and pulverized to be remade into another part via metal injection moulding (MIM) in this work. MIM usually produces complex, intricate, and high-quality parts in large quantities (10,000< units). Thus, carving a clear path for recycling aluminium alloy through MIM is in value added territory. Not to mention that aluminium MIM in general has yet to be commercialised as this is still an on-going research due to the intriguing properties of aluminium in the efforts to be sintered. Moreover, as palm stearin (PSr) has successfully been used in singularity instead of the common practice of using a system of binders, this work takes two steps more along the path of greener manufacturing. This is because aluminium and PSr themselves have relatively low melting ranges (~400°C-700°C and ~55°C-70°C, respectively) which lowers the typical working temperature of injection moulding. Subsequently, the standalone PSr binder is capable of providing pseudo-plasticity which is a substantial factor in the succession of injection moulding. Mainly, this work aims to characterise AAS powder through planetary ball milling purged with inert gas (argon) for manufacturing via MIM. The average particle size is ~13 μm, due to the gas gauging down the chamber temperature, resisting agglomeration. The powder produced are irregular in shape and generally bulky, with a broad distribution of particle sizes. These characteristics assists in particulate interlocking, contributing to green part strength. Next, the pulverised AAS (PAAS) is mixed with 100vol% of PSr to form feedstock with three powder loadings (63 vol%, 65 vol% and 67 vol% PAAS). However, only the 65 vol% of PAAS is selected for further work since it provided the highest packing density with consistent fluidity as pressure increases. Consequently, the PAAS feedstock is successfully injected within 65°C to 70°C with a corresponding injection pressure of 300 kPa to 400 kPa. Lastly, comes the binder removal and consolidation of PAAS particulates through thermal debinding and sintering, respectively. This is where the effects of different heating rate and soaking parameters for both thermal debinding and sintering are varied and evaluated. The proposed ideal thermal debinding heating rate should range between 0.3 to 0.5 ºC/min, with holding duration kept within 30 to 120 minutes and soaking temperature between 420ºC to 550ºC. While for sintering, heating rate should range between 1 to 3 ºC/min, holding duration kept between 50 to 80 minutes, and holding temperature within 575ºC to 580ºC. As such, working samples for further research work or testing can be produced as the plausibility of particulate consolidation is apparent.
Metadata
Item Type: | Thesis (Masters) |
---|---|
Creators: | Creators Email / ID Num. Yussoff, Sarah Balqis 2017757495 |
Contributors: | Contribution Name Email / ID Num. Thesis advisor Mohd Nor, Nor Hafiez UNSPECIFIED |
Divisions: | Universiti Teknologi MARA, Shah Alam > College of Engineering |
Programme: | Master of Science (Mechanical Engineering) – EM750 |
Keywords: | aluminium, alloy, automotive |
Date: | 2023 |
URI: | https://ir.uitm.edu.my/id/eprint/81946 |
Download
![[thumbnail of 81946.pdf]](https://ir.uitm.edu.my/style/images/fileicons/text.png)
81946.pdf
Download (200kB)
Digital Copy
Physical Copy
ID Number
81946
Indexing
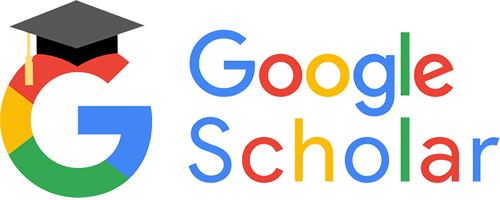
