Abstract
Liquefaction of Mukah Balingian (MB) coal was successfully performed in ordinary one stage semi-continuous solvent flow reactor system at various temperatures (300 - 450 °C), various solvent flow-rates (1- 5 ml/min), and various reaction times (30-6 0 min) with fixed pressure at 4 MPa and tetralin as the solvent. The coal sample was ground into small particles before it being liquefied. The best condition for the solvent flow reactor was found at temperature of 420 °C, solvent flow rate of 1 ml/min, and reaction time of 60 min. The coal conversion and oil+gas yield obtained at those conditions were 79.1 % and 60.1 %, respectively. Despite the ability of adding fresh solvent into the extraction process, the conversion of oil+gas still considered to be low compare with percentage of coal extract using batch-wise reactor. This may due to the reactor enabled the re-polymerization to occur during liquefaction process which led to more formation of heavier coal extracts. One possible option to increase the oil+gas yield is by applying catalyst that will break up the heavier coal extracts into small molecular weight compounds. By using normal impregnated into the coal sample, the coal liquefaction residue (CLR) might be contaminate with the catalyst which may influence the ability of the CLR to be further used as combustion material. Thus, the second reactor was introduced consisted of NiSiC>2 as the catalyst that will separate the coal sample and the catalyst. The Ni catalyst was prepared using simple impregnation method. The application of response surface methodology (RSM) was chosen because of its ability to decrease the number of experiments, time and material resources due to its capacity to evaluate important test that requires achieving the optimum result. The system shown that the optimum conditions were 1.12 ml/min of solvent flow-rate, 30 min of reaction time and 5 wt.% of Ni loading that gave out response value for oil+gas yield of 70.25 %. Durability tests were done in order to figure out the ability of the catalyst to maintain its performance. Such tests were done by repeatedly used the same catalyst over and over again while observing the conversion of product distribution yields. The result showed that the NiSiCh can hold up to 5th run before the percentages started to depleted. It may be because of carbon deposited on the surface to cover the active sites.
Metadata
Item Type: | Thesis (Masters) |
---|---|
Creators: | Creators Email / ID Num. Safian, Muhammad Taqi-Uddeen 2007131451 |
Contributors: | Contribution Name Email / ID Num. Thesis advisor Ismail, Khudzir UNSPECIFIED |
Divisions: | Universiti Teknologi MARA, Shah Alam > Faculty of Applied Sciences |
Programme: | Master of Science - AS780 |
Keywords: | coal, Mukah, reactor |
Date: | 2012 |
URI: | https://ir.uitm.edu.my/id/eprint/79007 |
Download
![[thumbnail of 79007.pdf]](https://ir.uitm.edu.my/style/images/fileicons/text.png)
79007.pdf
Download (173kB)
Digital Copy
Physical Copy

ID Number
79007
Indexing
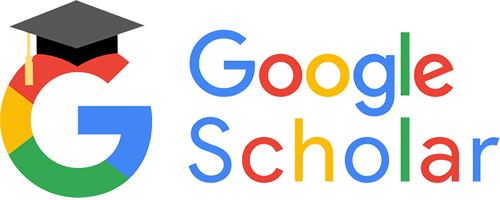
