Abstract
Electro-textile, known as e-textile is a conducting fabric that enables digital computing or electronic devices to be integrated into them to form wearable systems. Thus, e-textile antenna is designed to support many wearable applications, including tracking, navigation, mobile computing, public safety, entertainment, and wireless communication. The conventional textile-based antenna uses copper tape and copper foil as the radiating element. However, the usage of copper tape and copper foil leads to sustainability issues as these materials can be easily detached after being worn and washed several times. In terms of accuracy, previously, the conventional conductive textile antenna suffered some design issues where the measurement data were not in good agreement with the expected result. This scenario happened due to the inaccurate modelling during simulation where a solid copper sheet with different electrical properties was used to represent e-textile layer. Besides, for some conductive textiles, the electrical properties are also influenced by the interweaving ratio of the weaving pattern. Other than that, mechanical deformations such as bending due to human’s small movements can also affect the antenna resonant frequency, as it will be detuned when the antenna is bent. Therefore, a self-manufactured conductive textile with a more structurally practical structure for antenna design is proposed in this research work. To improve the design accuracy, the structure of e-textile was developed using TexGen software during antenna simulation stage. A performance analysis of the e-textile based on different weaving patterns such as plain, satin and twill was also conducted. Other than that, optimization is performed to produce an optimum 1.575 GHz GPS antenna that can operate under deformed condition. In this research, two conductive textiles; copper covered yarn and copper core sheathed yarn were constructed using hollow-spindle-spinning technique. The developed fabric structures were designed through physical model using TexGen and also based on accurate electrical properties using I-V probe method. Various designs of textile antennas were simulated and measured under E-plane and H-plane bent conditions to validate the reliability of the antenna under deformed condition. An antenna with a defected ground structure (DGS) is developed to solve the bending problem. Through the analysis, copper covered is the best conductive yarn with the copper-to-polyester composition ratio of 82.90% to 16.36%. Meanwhile, satin is the best weaving pattern for conductive textiles with a conductivity of 9.26 x104 S/m. Based on the study, the bending on E-plane shows significant frequency detuning as compared to H-plane. The implementation of DGS has increased the antenna bandwidth from 74 MHz to 226 MHz. Therefore, by having a wider bandwidth, the antenna can operate at the desired frequency even during bending. The antenna performance was verified through the simulation and measurement results. In conclusion, this project has minimized the frequency detuning effect during bending through DGS implementation, which is a common issue in all textile antennas. Plus, the development of the new conductive textile provides an integrated solution for the antenna and fabric as one module. An alternative way to simulate an accurate fabric structure of the textile antenna is also shown in this project.
Metadata
Item Type: | Thesis (PhD) |
---|---|
Creators: | Creators Email / ID Num. Zaidi, Norsyahirah Izzati 2016380309 |
Contributors: | Contribution Name Email / ID Num. Thesis advisor Abd Rahman, Nurul Huda (Ir. Dr.) UNSPECIFIED |
Subjects: | T Technology > TK Electrical engineering. Electronics. Nuclear engineering > Electronics > Apparatus and materials > Antennas |
Divisions: | Universiti Teknologi MARA, Shah Alam > College of Engineering |
Programme: | Doctor of Philosophy in Electrical Engineering |
Keywords: | Wearable technology; textile antenna; dielectric; electro-textile |
Date: | June 2021 |
URI: | https://ir.uitm.edu.my/id/eprint/61066 |
Download
![[thumbnail of 61066.pdf]](https://ir.uitm.edu.my/style/images/fileicons/text.png)
61066.pdf
Download (40kB)
Digital Copy
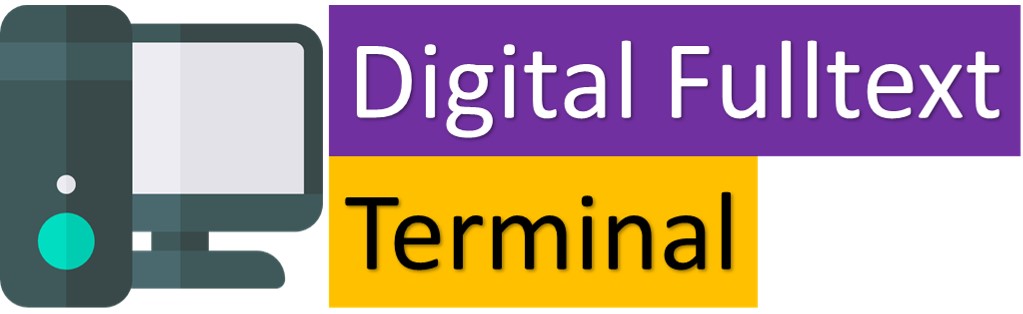
Physical Copy
ID Number
61066
Indexing
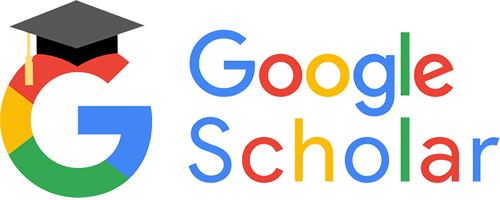
