Abstract
Nowadays, applications of metallic material are facing higher performance requirements due to constant exposure to the friction and wear, adversely affecting global manufacturing productivity performance and high maintenance costs. This study focused on the effect of surface attrition treatment towards the boron diffusivity and the wear mechanism of boronized compacted graphite iron. The research was conducted by introducing paste boronizing to replace conventional powder boronizing medium to produce better boron atom diffusion. Boronized samples with thicker boride layer and better hardness were thus selected to undergo surface attrition using the shot blasting method. The optimization of boronizing parameters between 800℃ to 950℃ and 4 to 10 hours after the surface attrition method were selected by using the Taguchi Method. Finally, the wear characterization of the optimized boronizing process parameter was studied. Analysis of the microstructure and thickness of the boride layer was performed using optical microscopy, scanning electron microscopy (SEM) analyzer and energy dispersive X-Ray (EDX) spectrometry. Other tests such as density, microhardness, Rockwell adhesion, pin on disk, slurry erosion and surface roughness were conducted. As a result, applying boronizing paste as the medium with paste thickness range within 3 to 7 mm resulted in improvement in boride layer thickness and microhardness compared to powder boronized samples. The application of surface attrition with 5 bar blasting pressure increased the boride layer thickness and microhardness up to 63% and 24% respectively, compared to boronized samples without surface attrited. The value of boron activation energy of boronized compacted graphite iron after surface attrited is 240.82 kJ mol−1 and the frequency factor is 3 x 102 (cm2/s). The adhesion strength quality of samples surface attrited with paste boronized at 800℃, 900℃, 950℃ for 6 hours and 850℃ for 8 hours were sufficient as it fits HF1 to HF4 category. Samples with the highest boronizing temperatures of 950℃ for 6 hours lead the superior wear resistance and microhardness properties. The result was mainly because of the implementation of surface attrition treatment that resulted in the grain refinement that allowed a deeper boride layer to be diffused into the surface of the as-cast sample. The developed boronizing methods lead to the improvement of properties such as hardness and wear resistance of compacted graphite iron. The established of an empirical model from this study make it possible to predict the boride layer thickness for industrial application include drive shafts, piping components, pulleys, braking disc, metal stamping machines and other machines parts.
Metadata
Item Type: | Thesis (PhD) |
---|---|
Creators: | Creators Email / ID Num. Muhammad Yusof, Khalissah 2015256064 |
Contributors: | Contribution Name Email / ID Num. Thesis advisor Abdullah, Bulan (Associate Professor Ir. Ts. Dr.) UNSPECIFIED |
Subjects: | T Technology > TJ Mechanical engineering and machinery > Mechanical movements |
Divisions: | Universiti Teknologi MARA, Shah Alam > Faculty of Mechanical Engineering |
Programme: | Doctor of Philosophy in Mechanical Engineering |
Keywords: | Metal alloys; cast iron; graphite iron; case hardening; boronizing; surface attrition; wear resistance; wear rate; friction |
Date: | September 2020 |
URI: | https://ir.uitm.edu.my/id/eprint/60732 |
Download
![[thumbnail of 60732.pdf]](https://ir.uitm.edu.my/style/images/fileicons/text.png)
60732.pdf
Download (39kB)
Digital Copy
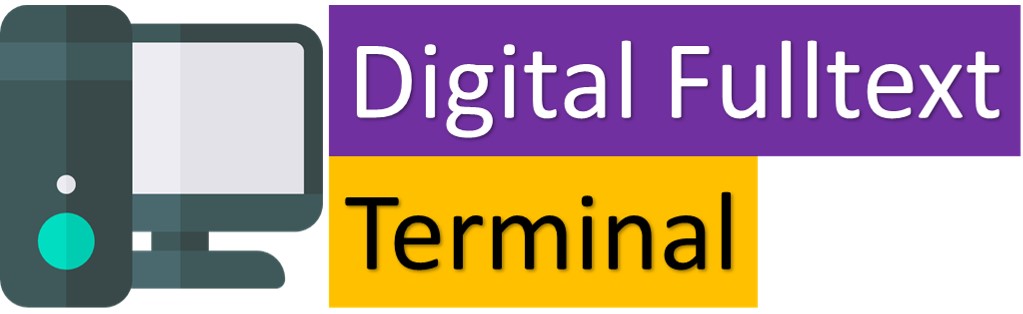
Physical Copy
ID Number
60732
Indexing
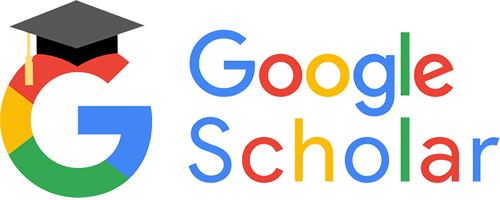
