Abstract
A great limitation in producing porous structure on semiconductor surfaces is due to the lack of reliable techniques for fabrication of uniform pore morphology. In the current technique of direct current electrochemical etching (DCPEC), the challenge is in controlling the etching parameters to obtain uniform porous structure. Hence, a possible way to control the etching parameters is by introducing the pulse etching technique whereby the current can easily be controlled by the ON and OFF times and eventually will result in uniform pore morphology. Therefore, the objective of this research is to synthesize the porous structure porous silicon (P-Si) and porous GaN (P-GaN)) by novel integrated pulsed electrochemical etching (iPEC) method and characterize its structural and optical properties. The work of this research was divided into two part which was firstly the formation of P-Si by DCPEC and iPEC, and in the second part was the formation of P-GaN using DCPEC and iPEC. An introduction of delay time coupled with pulsed (applying Ton and Toff) electrochemical etching was utilized to form uniform P-GaN under various parameter. In the first part, the P-Si etched by the DCPEC technique produced a square-like pore while the iPEC technique formed a mix of square and crossed shape pores. This proved that the pore formed were rely strongly on the etching technique applied. Then, the Si samples were etched by using iPEC etching techniques under various current densities. The obtained P-Si samples showed strong relationship on the etching current density. The sample etched with current density of 20 mA/cm2 exhibited 24% porosity, which is highest compare to other current density sample. Moreover, all P-Si samples observed have shown an increase in the bandgap value from bulk Si, indicating that the porous structure offers shift of bandgap to the visible spectrum. The porous samples produced a nanostructures pore with estimated diameter of 7.74 nm, 7.79 nm and 7.84 nm from 10 mA/cm2, 20 mA/cm2 and 30 mA/cm2 samples, respectively. For the second part, the P-GaN was successfully fabricated using UV-assisted DCPEC electrochemical etching techniques with an application of lower power for UV light. From the results, the technique produced similar shapes but different in pore sizes, uniformity and porosity corresponding to the variations of current density applied during anodization. This proved that the current density affected the porous formation on the GaN surface and the most preferred current density in forming a high densities pore is 80 mA/cm2. For the optical characteristics, both Raman and PL spectra intensity increased with the current density. Next, by using the optimum current density gained (80 mA/cm2), the P-GaN was fabricated by iPEC and delayed iPEC etching techniques respectively. The difference between iPEC and delayed iPEC is the application of delay time before starting the electrochemical etching process. From the FESEM result, there is significant different by applying delayed iPEC to fabricate P-GaN. Delayed iPEC pore sample created a smaller pore with a diameter approximately ~29nm with highest porosity of 80%. The PL peak intensity of the delayed iPEC sample was higher compared to iPEC sample. This pinpoint that the porosity has highly impact on the PL peak intensity. In general, the research outcomes (P-Si and P-GaN) from the DCPEC and iPEC techniques had shown potential tuneable wavelength (from UV to visible spectrum) by varying the etching parameters suitable for the fabrication of enhanced optoelectronic devices.
Metadata
Item Type: | Thesis (Masters) |
---|---|
Creators: | Creators Email / ID Num. Mohd Razali, Nurul Syuhadah 2016204746 |
Contributors: | Contribution Name Email / ID Num. Thesis advisor Abd Rahim, Alhan Farhanah (Ir. Dr.) UNSPECIFIED |
Subjects: | Q Science > QC Physics > Electricity and magnetism |
Divisions: | Universiti Teknologi MARA, Shah Alam > Faculty of Electrical Engineering |
Programme: | Master of Science (Electrical Engineering) |
Keywords: | Silicon; GaN; porous; electrochemical etching |
Date: | December 2021 |
URI: | https://ir.uitm.edu.my/id/eprint/60614 |
Download
![[thumbnail of 60614.pdf]](https://ir.uitm.edu.my/style/images/fileicons/text.png)
60614.pdf
Download (60kB)
Digital Copy
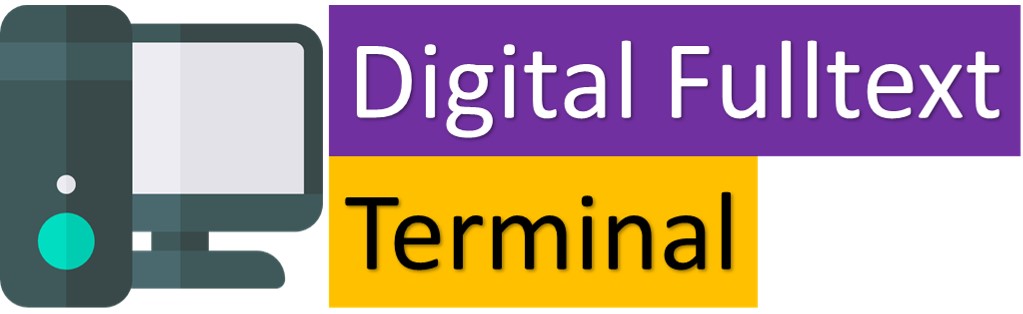
Physical Copy
ID Number
60614
Indexing
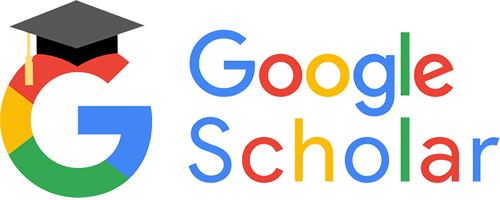
