Abstract
Sensitive automated reaction from the sensory system is most important in fulfilling the requirement of the intelligent control system. Hence, there are many related studies regarding developing the hardware of the system. The effect of the fast detection of the sensor through the high sensitivity of the airflow sensor has enable the system to identify and analyse the behaviour of the user in higher accuracy compared to the conventional system. Within the scope of airflow sensitivity, the problem of the conventional airflow sensor is its narrow range of detection and the approach used for detection. The necessity and approach for dynamic airflow sensor is lacking because of the limited information and research that can be done in past research due to lack of technology such as analysis software. Hence, this research proposed a separation between two parts in the airflow sensor in altering the velocity impact that have been inquired in purpose, while a few investigations in relations to determine the pressure contour in the analysis. The analysis have been done by using Computational Fluid Dynamics (CFD) to explore the possible outcomes such as producing the simulation of the airflow, pressure streamline, deformation and performance of the new product. This simulation is performed in the ANSYS program software. Thus, this study consequently intends to focus on detection of the high sensitivity of the airflow movement by distinguishing the high and low velocity impact. The data of the airflow movement will be mapped accordingly in order to produce a prototype that is capable to detect the airflow with more than 90% high sensitivity performance. The approach in mapping need to be verified through series of testing in the wind tunnel to ensure the data collected can be categorized with the speed inside the wide tunnel. The flap structure has been divided into two main categories with a different purpose. The detection method is by using voltage divider rule in recording the converted voltage on the bending flap structure during the testing stage in the simulation and wind tunnel. The findings of the research shows that the detection was done by bending moment method to meet the requirement of the objectives stated in the research. Improvement on the design was done for the detection structure to increase the sensitivity and characterize the different speed of the airflow. Based on the pressure characterization analysis, the lower velocity gap (LG) and high velocity gap (HG) are in the range of 0.5 to 0.1 mm. While for the lower velocity flap thickness (LT) and high velocity flap thickness are maintained to the original design of 1 mm and 2mm respectively. As for bending moment analysis, the lower velocity flap thickness (LT), lower velocity gap (LG) and high velocity gap (HG) are remained constant with 0.4 mm, 0.5 mm and 1 mm respectively. The range of thickness for high velocity flap (HT) is between 2.00 mm and 3.04 mm. The best possible thickness that gave high total deformation (13.675mm) is 3.02 mm. The result also shows that the airflow has been mapped accordingly and justify the result in the simulation as required to achieve the objectives of this research. In testing stage, low velocity flap recorded the range from 11 b to 32 b for airflow speed from 0 km/h to 60 km/h. Meanwhile, high velocity flap recorded the range from -11.7 b to -7.9 b for airflow speed from 60 km/h to 110 km/h. Implications of the results and future research directions which the prototype was able to measure the airflow changes with high sensitivity airflow detection and broad range of speed after the characterization of the airflow speed had been achieved. The results presented in this study may facilitate improvements in the technology of the moving object by integrating the new sensor in achieving high sensitivity airflow detection while in motion.
Metadata
Item Type: | Thesis (PhD) |
---|---|
Creators: | Creators Email / ID Num. Amari, Mohamad Dzulhelmy 2016832934 |
Contributors: | Contribution Name Email / ID Num. Thesis advisor Che Abdullah, Sukarnur (Dr.) UNSPECIFIED |
Subjects: | T Technology > TJ Mechanical engineering and machinery > Microfluidics and microfluidic devices |
Divisions: | Universiti Teknologi MARA, Shah Alam > Faculty of Mechanical Engineering |
Programme: | Doctor of Philosophy in Mechanical Engineering |
Keywords: | Data characterization; mapping validation; macrofluidic dynamic airflow; sensor |
Date: | January 2021 |
URI: | https://ir.uitm.edu.my/id/eprint/59827 |
Download
![[thumbnail of 59827.pdf]](https://ir.uitm.edu.my/style/images/fileicons/text.png)
59827.pdf
Download (239kB)
Digital Copy
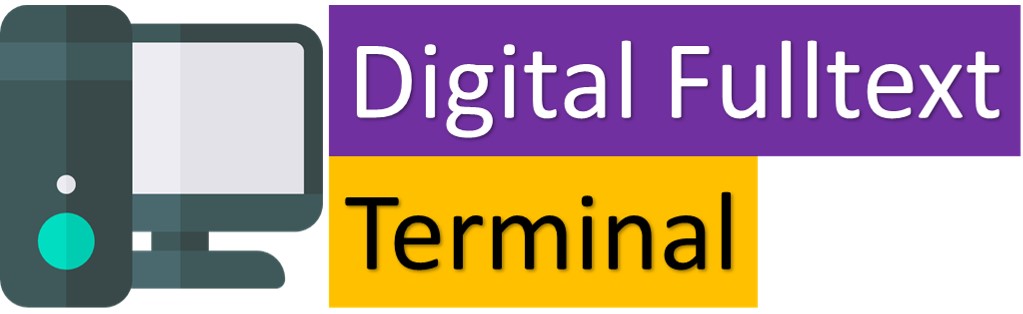
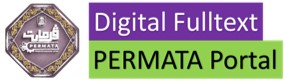
Physical Copy
ID Number
59827
Indexing
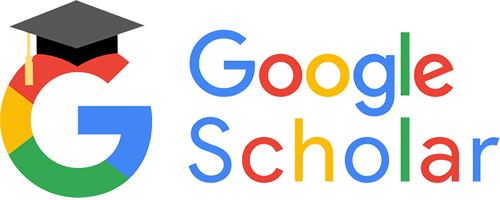
