Abstract
Mechanical joints are commonly used in engineering application to form assembled structures such as car Body in White (BiW) and aerospace structures. Understandably, the mechanical joints have a significant effect to the dynamic characteristic of assembled structure because each of the joint in the structure has its own joint properties such as slip factor, contact surface and non-linearity. Therefore, the overall dynamic characteristics of the jointed structure highly rely on the joints. On the other hand, finite element analysis (FEA) is a tool that commonly used by engineers to model and to reduce the number of physical prototypes in order to develop better products such as automotive parts. However, it has been found that there are huge discrepancies between the finite element analysis and experimental data due to invalid assumptions and simplification in modelling the joints in the finite element analysis. Consequently, the initial finite element model of the structure needs to be improved as close as possible to the experimental data. The aim of this research is to investigate the potential element connectors that can be used to represent the joints for spot weld and adhesive joints. The reliability of potential connector elements were quantified by comparing the predicted result calculated from commercial finite element analysis package with the experimental data. There were four types of element connectors used to model the adhesive joints and spot welds namely, RBE2, ACM2, CWELD and CWELD ELPAT and they were constructed based on three types of the case studies namely Case Study 1, Case Study 2 and Case Study 3. In the experimental work, the shaker and the roving accelerometers method were used to measure the modal parameters of the structure. The comparison reveals that the Case Study 3, which is the combination of element connectors Type 2 (ACM2) and Type 4 (CWELD ELPAT) have shown a better capability to represent the joints of the assembled structure with total error was 31.98 % while other finite element models, such as Case Study 1 and Case Study 2 with total error recorded were 263.23 % and 33.82 % respectively. The finite element model of Case Study 3 was then used in the optimisation method using model updating with MSC NASTRAN SOL200 algorithm to compute the sensitivity analysis based on the input parameters of the spot weld and adhesive joints and the body of the car hood structure. The predicted results obtained from the optimisation method has shown a significant achievement with total error was managed to reduce from 31.98 % to 19.92 %. The results reveal that, the predicted model using Case Study 3 procedure was the most appropriate to represent as spot weld and adhesive joints in the car hood structure. Furthermore, the optimisation method using model updating was successfully implemented and improving the correlation of the predicted results with experimental counterpart.
Metadata
Item Type: | Thesis (Masters) |
---|---|
Creators: | Creators Email / ID Num. Sulaiman, Mohamad Shamsul Azraf 2015416338 |
Contributors: | Contribution Name Email / ID Num. Thesis advisor Yunus, Mohd Azmi (Ir. Dr.) UNSPECIFIED Thesis advisor Abdul Rani, Muhamad Norhisham (Dr.) UNSPECIFIED |
Subjects: | T Technology > TJ Mechanical engineering and machinery |
Divisions: | Universiti Teknologi MARA, Shah Alam > Faculty of Mechanical Engineering |
Programme: | Master of Science (Mechanical Engineering) |
Keywords: | Finite Element Method (FEM); Structural Joint Modelling |
Date: | May 2020 |
URI: | https://ir.uitm.edu.my/id/eprint/59650 |
Download
![[thumbnail of 59650.pdf]](https://ir.uitm.edu.my/style/images/fileicons/text.png)
59650.pdf
Download (291kB)
Digital Copy
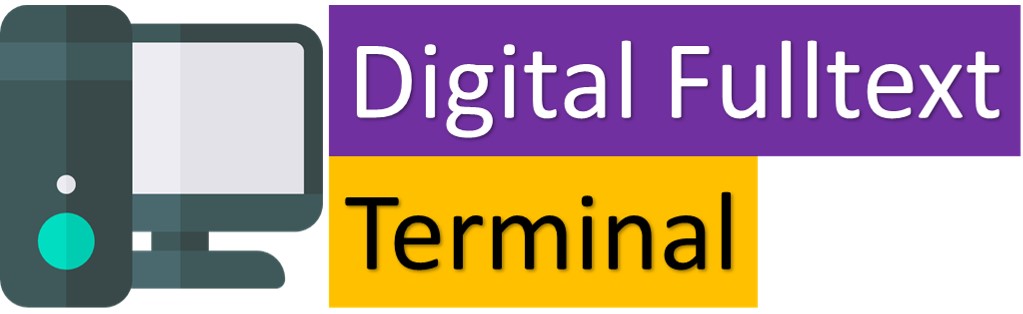
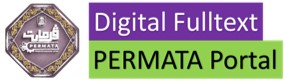
Physical Copy
ID Number
59650
Indexing
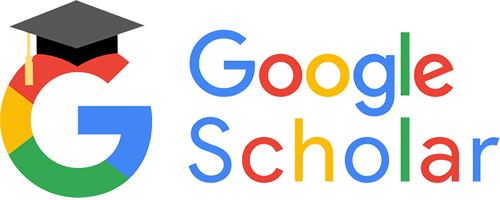
