Abstract
The aim of this paper is to diagnose the faults that occurred in rotating machinery. Pattern recognition technique was implemented using three main steps of fault diagnosis; feature extraction, dimensionality reduction and fault classification. This paper focuses on the faulty bearing which mainly caused by mass imbalance and axis misalignment. Vibration signal that obtained from the rotating machinery is extracted by using non-parametric or parametric method to get the power spectrum density (PSD). Principal Component Analysis (PCA) is then introduced to reduce the complexity as well as smooth the classification process. By analyzing the vibration signal obtained from the test rigs (rigs that are built to demonstrate the effect of faults in rotating machinery), it gives solid information concerning any faults within
the rotating machinery.
Metadata
Item Type: | Research Reports |
---|---|
Creators: | Creators Email / ID Num. Othman, Nor Azlan UNSPECIFIED Damanhuri, Nor Salwa UNSPECIFIED Hamzah, Norhazimi UNSPECIFIED |
Subjects: | T Technology > TK Electrical engineering. Electronics. Nuclear engineering T Technology > TK Electrical engineering. Electronics. Nuclear engineering > Production of electric energy or power |
Divisions: | Universiti Teknologi MARA, Pulau Pinang > Permatang Pauh Campus |
Keywords: | Rotating Machinery, Power Spectrum Density (PSD), Principal Component Analysis (PCA) |
Date: | December 2009 |
URI: | https://ir.uitm.edu.my/id/eprint/42033 |
Download
![[thumbnail of 42033.pdf]](https://ir.uitm.edu.my/style/images/fileicons/text.png)
42033.pdf
Download (40kB)
Digital Copy
Physical Copy

ID Number
42033
Indexing
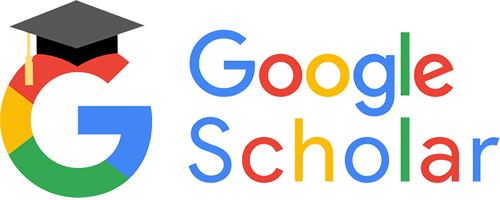
