Abstract
Metal injection molding (MIM) is a promising technique for fabricating porous metal parts as it can produce complex parts with a controlled porous structure. This research is focused on producing porous copper parts using MIM process where sodium chloride (NaCl) is used as the space holder material. The volume fraction of NaCl was set to 20 vol% to replace the copper volume fraction, while the binder volume fraction was kept constant. Three powder loadings were used which are 59, 61 and 63 vol% based on critical powder loading volume percentage (CPVP). The feedstock is prepared by using sigma blade mixer and the feedstock shows constant torque values which indicate homogeneous mixing during torque analysis. The rheological behavior of the feedstock was investigated by using capillary rheometer machine where all feedstock exhibit pseudo plastic behavior. The feedstocks were analyzed further in terms of flow behavior index («), activation energy (E) and mold ability index (a). All feedstock produced acceptable value and suitable for injection molding process. Taguchi method of Lciorthogonal array was used as a tool in optimization of MIM parameters for the highest green strength. Parameters that were optimized were powder loading, mixing temperature, mixing speed and injection temperature. Results from analysis of variance (ANOVA) shows that powder loading has the highest contribution for green strength with 61.81% followed by injection temperature (30.01%), mixing speed (7.48%) and mixing temperatures (0.69%). Optimum parameters from Taguchi method were used and injection molding process was carried out to produce tensile bar shape samples. The effect of different sintering heating rate towards properties of sintered parts was studied. As a result, sintering heating rate of 0.5°C/min shows positive results in terms of shrinkage, density and thermal conductivity compared to others (1.0 and 0.75°C/min). Sintered parts at heating rate of 0.5°C/min produced uniform shrinkage (1.42%), high density (6.51g/cm3 ), high thermal conductivity (429.09 W/mk) with low porosity (25.59%). The optimized sintered part can improve heat exchanger application as the production of porous copper part using MIM technique can form small complex shape with high thermal conductivity in less weight ratio.
Metadata
Item Type: | Thesis (Masters) |
---|---|
Creators: | Creators Email / ID Num. Kamal Bahrin, Mohammad Dahar 2013715527 |
Contributors: | Contribution Name Email / ID Num. Thesis advisor Wahab, Nor'Aini UNSPECIFIED |
Subjects: | T Technology > TP Chemical technology > Molding (Chemical technology) |
Divisions: | Universiti Teknologi MARA, Shah Alam > Faculty of Mechanical Engineering |
Programme: | EM750 |
Keywords: | Metal injection molding (MIM), porous, molding |
Date: | 2018 |
URI: | https://ir.uitm.edu.my/id/eprint/38441 |
Download
![[thumbnail of 38441.pdf]](https://ir.uitm.edu.my/style/images/fileicons/text.png)
38441.pdf
Download (193kB)
Digital Copy
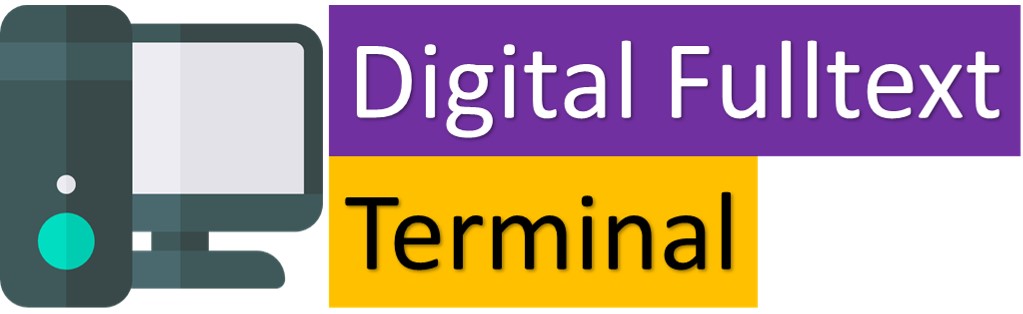
Physical Copy

ID Number
38441
Indexing
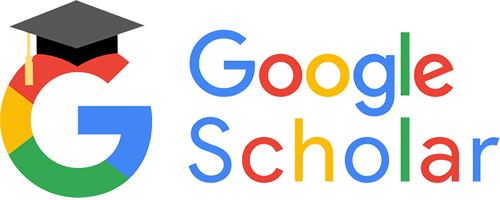
