Abstract
Synthetic jet is a pumping mechanism device that been used as a cooling method for electronic devices. It is a device that formed by suction and ejection of fluid that produce by oscillating diaphragm inside the cavity. The advantages of the synthetic jet are produced higher heat transfer coefficient (h) compared to the fan system and will reduce the power consumption and increase the consistency. Besides, it helps to enhance the thermal performance and lower noises as well as reduce the flow bypass and increases the local heat transfer from the heat sinks. This arrangement also does not require additional fluid circuit which makes it simpler compared with other methods. The common cooling system used which is fan-type has numerous disadvantages such as noise produce from the fan, the weight of the fans itself, need to use an air filter to prevent dust from entering the case to avoid the dust from clogging up the internal components. 3D printing has been used to fabricate the synthetic jet model to determine heat transfer coefficient. The maximum heat transfer cavity depth for the synthetic jet is 1 mm compared with 2 mm, 3 mm, 4 mm and 5 mm. Four different types of nozzle shape have been tested which are circular, diamond, triangle and square at various distance from the heated surface. The experiment also was conducted with frequency range 300 Hz to 700 Hz and the effective value of frequency for the maximum heat removal is 500 Hz. The result shows that circular nozzle shape with 3 mm diameter at 3 cm distance with 500 Hz frequency has maximum heat transfer coefficient. High velocity fluid is obtained at circular shape with 3 mm diameter nozzle of 1 cm distance. As the conclusion, maximum heat transfer coefficient was at 500 Hz which is at resonance frequency and higher diameter nozzle has low heat transfer coefficient with low fluid velocity.
Metadata
Item Type: | Student Project |
---|---|
Creators: | Creators Email / ID Num. Maswan, Nor Maisarah 2013275934 |
Contributors: | Contribution Name Email / ID Num. UNSPECIFIED Sh Abdul Nasir, Ir. Sh Mohd Firdaus UNSPECIFIED |
Subjects: | T Technology > TJ Mechanical engineering and machinery T Technology > TJ Mechanical engineering and machinery > Hydraulic machinery |
Divisions: | Universiti Teknologi MARA, Pulau Pinang > Permatang Pauh Campus > Faculty of Mechanical Engineering |
Programme: | Bachelor of Mechanical Engineering (Manufacturing) (Hons.) |
Keywords: | Synthetic Jet, Heat Transfer Coefficient, Cooling System |
Date: | July 2016 |
URI: | https://ir.uitm.edu.my/id/eprint/35083 |
Download
![[thumbnail of 35083.pdf]](https://ir.uitm.edu.my/style/images/fileicons/text.png)
35083.pdf
Download (182kB)
Digital Copy
Physical Copy

ID Number
35083
Indexing
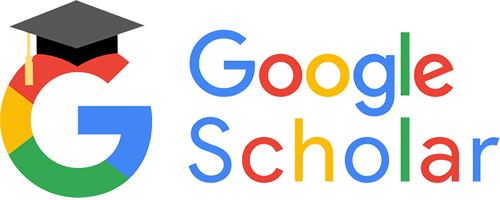
