Abstract
Eddy current testing (ET) is one of the Non destructive testing (NDT) techniques for the detection and evaluation of surface and sub-surface defects in electrically conducting materials. This technique is the most effective technique for the assessment of heat exchanger tubes in monitoring the integrity of a heat exchanger system. In performing the eddy current inspection , probe is the most important component in acquiring information from the heat exchanger system. It is the main factor that determines the success of an eddy current testing for optimum and reliable inspection results. This research work covers the experimental and numerical approach in fabricating an eddy current probe for tube inspection . The aim of the research is to study the physics and engineering parameters which can enable us to produce eddy current probes with the focus of studying the probe coil configuration that affect its sensitivity and resolution for eddy current testing. With the achievement in fabricating an eddy current probe that fulfill the requirement of code and standards for tube inspection, the work is proceed in the study of the effect of inter-coil spacing and coil width to the probe sensitivity and resolution. The sensitivity and resolution of the fabricated probes have been studied by measurement of Vpp values and signal phase separation between internal groove defect (10) & external groove defect (00) wall loss at different intercoil spacing and different coil width. The results obtained by both experimental and numerical work have shown that with reduced inter-coil spacing and coil width, the sensitivity and the resolution of the fabricated probes will be increased thus giving a better inspection reliability and performance. This behavior is mainly attributed to the physical parameter of the probe geometry. With reduced spacing and coil width, the eddy current density becomes denser in the test specimen at a specific region. This reflects that the resistance for the eddy currents to flow in the sample is reduced and the phase will be increased. In addition, with reduced inter-coil spacing between the two coils, the mutual impedance of the two coils will become dominant thus a denser eddy current will be induced in the sample. In eddy current testing, defect detection is based on how the eddy current is disturbed in the sample , with more induced current , more current will be affected by the presence of a defect thus increase the sensitivity and the resolution of the probe. In this study, there are good agreement between the experimental data and numerical model in determining the reliable eddy current probe for engineering application.
Metadata
Item Type: | Thesis (Masters) |
---|---|
Creators: | Creators Email / ID Num. Zainal Abidin, Ilham Mukriz UNSPECIFIED |
Subjects: | T Technology > TK Electrical engineering. Electronics. Nuclear engineering > Electronics > Apparatus and materials T Technology > TK Electrical engineering. Electronics. Nuclear engineering > Electronics > Applications of electronics |
Divisions: | Universiti Teknologi MARA, Shah Alam > Faculty of Mechanical Engineering |
Programme: | EM 780 |
Keywords: | Probe, Eddy current testing (ET), Non destructive testing (NDT), Electrically conducting |
Date: | 2008 |
URI: | https://ir.uitm.edu.my/id/eprint/27601 |
Download
![[thumbnail of TM_ILHAM MUKHRIZ ZAINAL ABIDIN EM 08_5.pdf]](https://ir.uitm.edu.my/style/images/fileicons/text.png)
TM_ILHAM MUKHRIZ ZAINAL ABIDIN EM 08_5.pdf
Download (2MB)
Digital Copy
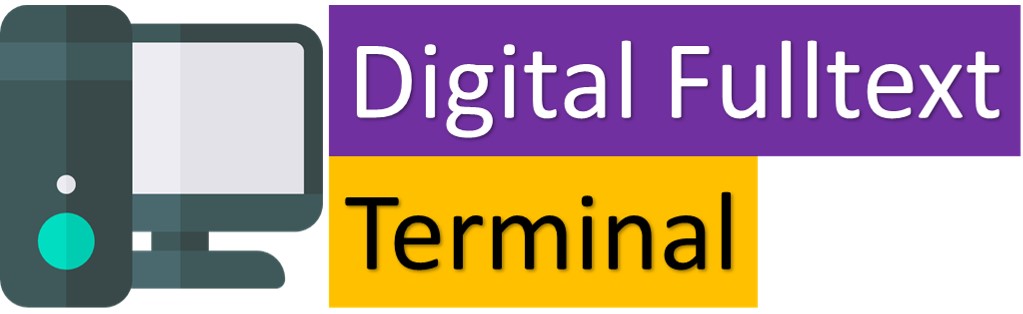
Physical Copy
ID Number
27601
Indexing
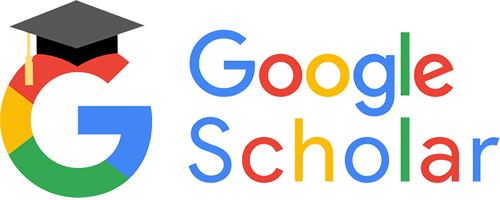
