Abstract
A new surface carburizing technique, superplastic carburizing (SPC), has been introduced and developed using thermo-mechanically treated duplex stainless steel (SPDSS) with fine microstructure as the superplastic material. SPC is a process which combines both the superplasticity phenomenon and carburizing process. Conventional carburizing (CC) was also carried out as a comparison to the SPC process using the as-received DSS with coarse microstructure and the fine microstructure DSS. Both SPC and CC processes were conducted in a tube furnace at temperatures ranging from 1123 K to 1223 K for 2, 4, 6 and 8 hours. Under the SPC process three different parameters which were the effect of initial pressures (25 MPa, 49 MPa and 74 MPa) applied, surface roughness with various grid paper (Ra = 0.3 urn, 0.1 urn and 0.03 um) and powder particle size (45 urn and 150 um) were also studied. Optical and electron microscope (SEM) investigations revealed microstructure indicating a dense, smooth and uniform morphology of carbide layer was formed on all carburized specimens. Fingerprint characterization of X-ray Diffraction (XRD) was done to confirm the existence of carbide phases. The carbide layer thickness formed on the surface of carburized DSS was shown to basically depend on the carburizing time and temperature. The higher the carburizing temperature and longer carburizing time was found to result in a thicker carbide layer. Carbide layer thickness obtained from conventionally carburized and superplastically carburized DSS was measured to be in the ranges from 14 \im to 40 urn and 15 um to 55 um respectively. The highest surface hardness was obtained through the SPC process which was determined to be in the range from 737 HV to 1400 HV under the highest initial pressure of 74 MPa while the surface hardness for both the as-received and fine microstructure DSS under the CC process was in the range of 555 HV to 1203 HV and 682 HV to 1303 HV respectively. The lowest activation energy was found and determined as 143.9 kJ/mol for the SPC process using the highest initial pressure of 74 MPa as compared to the initial pressure of 25 MPa and 49 MPa for which the activation energy was determined to be 171.3 kJ/mol and 168.9 kJ/mol respectively. The activation energy from the CC process for both as-received DSS and fine microstructure DSS was also determined to be 216.0 kJ/mol and 198.7 kJ/mol respectively. The carbide layer thickness obtained for different surface roughness conditions were in the range of 31 urn and 67 urn while the surface hardness achieved were in the range of 745 HV and 1445 HV. The effect of different powder particle size studies showed that the carbide layer thickness were in the range of 47.2 nm and 75.8 urn for the powder particle size of 150 |im used whereas a much thicker carbide layer which was in the range of 53 urn and 90 urn were obtained using powder particle size of 45 urn. The surface hardness obtained were in the range of 1041 HV to 1637 HV and 1284 HV to 1717 HV by using the 150 \im and 45 urn powder particle size respectively. The amount of carbon powder used for both CC and SPC processes were 55 g and 3 g respectively. This showed a 95 % reduction in powder consumption using the SPC process which indicates that this process is indeed an efficient and economical process as compared to the CC process.
Metadata
Item Type: | Research Reports |
---|---|
Creators: | Creators Email / ID Num. Nik Mohd Masdek, Nik Rozlin UNSPECIFIED Bahsan, Rosnadiah UNSPECIFIED |
Subjects: | T Technology > TP Chemical technology > Chemical engineering T Technology > TS Manufactures > Production management. Operations management |
Divisions: | Universiti Teknologi MARA, Shah Alam > Research Management Centre (RMC) > Institute of Research, Development and Commercialization (IRDC) |
Keywords: | Superplastic, Carburizing, Stainless Steel |
Date: | 2009 |
URI: | https://ir.uitm.edu.my/id/eprint/2613 |
Download
![[thumbnail of 2613.pdf]](https://ir.uitm.edu.my/style/images/fileicons/text.png)
2613.pdf
Download (142kB)
Digital Copy
Physical Copy

ID Number
2613
Indexing
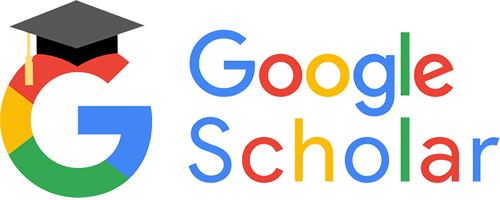
