Abstract
Resistance Spot Welding (RSW) process is commonly practiced in the automobile manufacturing industry where it is used mostly to weld the sheet metal to form the body of a car. The process tends to harden the base metal, which causes it to degrade. This affects the strength factor of the material as well as alters the physical and chemical properties of a sheet metal material. This is due to the heating applied above the materials recrystallization temperature, maintained at a certain temperature, and then cooled to ambient temperature. Attempts to improve the mechanical properties of the materials have been made via Post Weld Impact Treatment (PWIT) that consists of Low Blow Impact Treatment (LBIT) and Pneumatic Impact Treatment (PIT). Tensile-shear test and hardness test were performed as well as fatigue to ascertain the mechanical properties of the welded plate. Both methods of PWIT were then applied to the as welded RSW joint properties. The effects of PWIT on the tensile-shear load, hardness, and fatigue failure were also examined. Relating the mechanical properties with the process parameters of RSW are complex and tedious. Thus, applying the tri-objectives optimization method of low carbon steel reduces the tedious and time consuming conventional approach i.e using the single objective approach. Prior to the tests, the optimum process parameters of RSW joint were obtained using tri-objectives optimization approach as follows: the optimum welding time of 0.13s, electrode force at 2.82 kN, and welding current of 10.7 kA were obtained. The optimum parameters were then applied to the spot weld process. Low blow impact energy of 6 Joule was applied to the welded joint. An improvement of about 3% in tensile-shear load was indicated by the application of LBIT. The fusion zone in as-weld samples recorded hardness value of 211 HV while with the application of LBIT it increased up to 228 HV. Fatigue life in terms of prolonging the cycle lifetime also increased 3 times longer as the LBIT was applied. The tensile-shear load and fusion zone hardness of RSW joint after PIT using air pressure of 4 bar was improved by 8% and 27%, respectively. The number of cycles increased as PIT was applied on the welded joints. The fatigue life of RSW PIT was more than 1x106 cycles in load range of 3.2kN compared with as-weld at about 0.8 kN at 1x106 cycles. The RSW with subsequent PIT exhibited higher improvement as compared to RSW with LBIT. The improvements of the mechanical properties is envisaged as the result of the mechanical pulses produced by unique fluidic muscle conveyed to the surface of the RSW joint during PIT through hardened pins caused by plastic deformation and strain hardening. The strain hardening increases the ability of the material to withstand plastic deformation due to imparted dislocations. Hence, PIT applied in the upper and bottom surfaces of the joint were able to produce compressive residual stresses which is significantly deeper than the ones produced by LBIT. Application of post weld impact treatment on RSW hence improved the mechanical properties of the joint. The successful assessment and implementation of the PWIT, as a new method is capable to reduce necessary maintenance and increase the fatigue life of new and in service structures. The method is simple and easily applied to the welded joints and as a safe design approach in the automotive industries.
Metadata
Item Type: | Book Section |
---|---|
Creators: | Creators Email / ID Num. Ghazali, Farizah Adliza UNSPECIFIED |
Subjects: | T Technology > TK Electrical engineering. Electronics. Nuclear engineering > Electric heating. Resistance heating |
Divisions: | Universiti Teknologi MARA, Shah Alam > Institut Pengajian Siswazah (IPSis) : Institute of Graduate Studies (IGS) |
Series Name: | IPSis Biannual Publication |
Volume: | 14 |
Number: | 14 |
Keywords: | Abstract; Abstract of thesis; Newsletter; Research information; Doctoral graduates; IPSis; IGS; UiTM |
Date: | 2018 |
URI: | https://ir.uitm.edu.my/id/eprint/22215 |
Download
ABS_FARIZAH ADLIZA GHAZALI TDRA VOL 14 IGS 18.pdf
Download (6MB) | Preview
ID Number
22215
Indexing
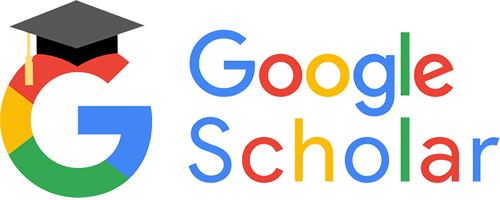
