Abstract
This thesis investigated the behaviour of angular distortion due to multipass GMAW process using finite element method (FEM). Various cases studies were conducted started with basic welding structure of butt and T-joint which is considered as the preliminary study to develop the fundamental numerical model. Further, the study was continued on the combined butt and T-joint to test the numerical model developed in the basic study of butt and T-joint before the models were applied on the ship panel application. Finally, the study was conducted on the ship panel (Laboratory Mock-up). In the simulation study, the distortion was analysed using 2D and 3D analysis based on thermo-elastic-plastic approach using FE software package SYS WELD 2010. It was found out that, 2D multipass analysis could be employed to obtain the fast average result of angular distortion while 3D multipass analysis to produce more accurate and complete results. To validate the simulation study, experimental investigations were conducted using fully automated robotic welding process. Almost all the simulation results were in good agreement with the experiments, except in 2D analysis on complex and large geometry. This result of the study indicates that the simulation study is reliable tool in predicting the welding induced distortion on the particular geometry and welding joint in this study. The effects of the clamping and welding sequence on distortion were also investigated in this study, and it was found out that the clamping condition and the welding sequences play a considerable factor in angular distortion.
Metadata
Item Type: | Thesis (Masters) |
---|---|
Creators: | Creators Email / ID Num. Lidam, Robert Ngendang 2010816504 |
Divisions: | Universiti Teknologi MARA, Shah Alam > Faculty of Mechanical Engineering |
Programme: | Master of Science |
Keywords: | Angular distortion; Multipass GMAW; Fem; Experimental validation |
Date: | October 2013 |
URI: | https://ir.uitm.edu.my/id/eprint/18453 |
Download
![[thumbnail of 18453.pdf]](https://ir.uitm.edu.my/style/images/fileicons/text.png)
18453.pdf
Download (127kB)
Digital Copy
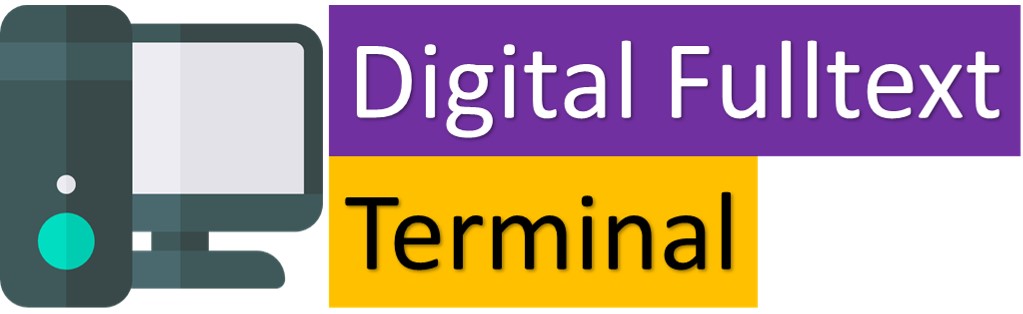
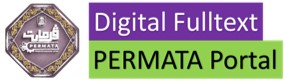
Physical Copy

ID Number
18453
Indexing
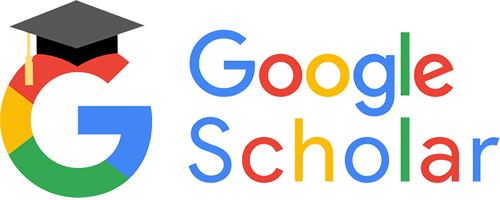
