Abstract
Thermal efficiency improvement, fuel consumption and pollutant emissions reduction from biodiesel fueled engines are critical requirements in engine research. In order to achieve these, a rapid and better air-fuel mixing condition is desired. The mixing quality of biodiesel with air can be improved by selecting the best engine design particularly combustion chamber design and injection system parameters. The present work investigates the effect of varying the piston bowl geometry on the air flow characteristics such as swirl velocity, Swirl Ratio (SR), and Turbulent Kinetic Energy (TKE) inside the engine cylinder. The piston’s bowl geometry was modified into several configurations that include Shallow depth combustion chamber (SCC), Toroidal combustion chamber (TCC), Shallow depth reentrant combustion chamber (SRCC) and Toroidal re-entrant combustion chamber (TRCC) from the standard Hemispherical combustion chamber (HCC), without altering the compression ratio of the engine. A commercially available CFD code STAR-CD was used to analyze the in-cylinder flow at different conditions. Flow conditions inside the cylinder were predicted by solving momentum, continuity and energy equations. The results confirmed that the piston bowl geometry had little influence on the in-cylinder flow during the intake stroke and the first part of compression stroke i.e. up to 300oafter suction TDC. However, the piston bowl geometry plays a significant role in the latter stage of the compression stroke i.e. beyond 300oafter suction TDC to compression TDC. The intensity of maximum swirl velocity at the end of compression stroke for TRCC was observed higher as 18.95 m/s and a strong recirculation was observed due to the geometry. Compared to baseline HCC the TRCC had higher, maximum swirl ratio and turbulent kinetic energy by about 28% and 2.14 times respectively. From the analysis of results, it was found that TRCC configuration gives better in-cylinder flows.
Metadata
Item Type: | Article |
---|---|
Creators: | Creators Email / ID Num. S. Jaichandar UNSPECIFIED A. Gunabalan UNSPECIFIED E. James Gunasekaran UNSPECIFIED |
Divisions: | Universiti Teknologi MARA, Shah Alam > Faculty of Mechanical Engineering |
Journal or Publication Title: | Journal of Mechanical Engineering (JMechE) |
UiTM Journal Collections: | UiTM Journals > Journal of Mechanical Engineering (JMechE) |
ISSN: | 1823-5514 ; 2550-164X |
Volume: | 13 |
Number: | 2 |
Page Range: | pp. 77-97 |
Keywords: | Diesel Engine, Combustion Chamber, Swirl Velocity, Swirl Ratio, Turbulent Kinetic Energy. |
Date: | 2016 |
URI: | https://ir.uitm.edu.my/id/eprint/17463 |
Download
![[thumbnail of AJ_S. JAICHANDAR JME 16.pdf]](https://ir.uitm.edu.my/style/images/fileicons/text.png)
AJ_S. JAICHANDAR JME 16.pdf
Download (1MB)
ID Number
17463
Indexing
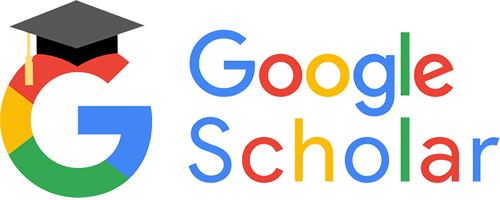
