Abstract
Computational fluid dynamics modeling was completed on the coal combustion to be implemented at Jimah Coal Fired Power Plant. The model was created in the Design Modeler and exported to computational fluid dynamics software called FLUENT. Non-premixed combustion model was chosen for coal combustion in order to better understand about the combustion and emissions from the process. Coal is used as a fuel in the combustion. The fuels were modeled with an empirical formula for coal from proximate and ultimate analyses. In FLUENT solver, coal contains species such as carbon, hydrogen, nitrogen, oxygen and sulfur. The oxidant use of the combustion process consists of 79% of oxygen and 21% of nitrogen. The measurement of mercury emissions in stack gas has an average value of 8.5 pg/Nm3. The mercury removal efficiency of the plant is 99.32% that shows the reduction of the mercury emissions due to the co-benefit of the electrostatic precipitator and flue gas desulfiirization. The measured value of mercury concentration at the outlet of the furnace is 1250 pg/Nm3. The model was tested to predict the temperature and species distribution from the coal combustion. The model is a 2-D furnace geometry with a width of 15.3 m and height of 48.5 m. The model has 5731 nodes and 5554 elements. The standard k-e model was used for turbulence model. Besides that, mercury as a pollutant emission also had been predicted from the model as a post-processing from the combustion. From the simulation results, the distribution of the flue gases such as carbon dioxide, carbon monoxide, water and oxygen can be observed. The temperature of the furnace is higher in the combustion zone and decreased when flows upward towards the outlet of the furnace. The three models of mercury had been implemented in Fluent that consist of One Step Model, Two Step Model and Detailed Wilcox Model. Besides that, the distribution of mercury products such as Hg, HgCl and HgCh show its behavior in the furnace. When comparing with the measurement at the outlet of the furnace, the Detailed Wilcox Model has given more accurate value with 1270 pg/Nm3, while One Step Model and Two Step Model give reasonably predicted values of 1000 pg/Nm3 and 1100 pg/Nm3 respectively.
Metadata
Item Type: | Thesis (Masters) |
---|---|
Creators: | Creators Email / ID Num. Mohamad, Nor Fadilah UNSPECIFIED |
Subjects: | T Technology > TP Chemical technology > Chemical engineering > Emulsions T Technology > TP Chemical technology > Chemical engineering > Fluidization |
Divisions: | Universiti Teknologi MARA, Shah Alam > Faculty of Chemical Engineering |
Programme: | Master of Science |
Keywords: | A computational fluid dynamics; Mercury emissions; Pulverized coal combustion |
Date: | 2015 |
URI: | https://ir.uitm.edu.my/id/eprint/15637 |
Download
![[thumbnail of TM_NOR FADILAH MOHAMAD EH 15_5.pdf]](https://ir.uitm.edu.my/style/images/fileicons/text.png)
TM_NOR FADILAH MOHAMAD EH 15_5.pdf
Download (10MB)
Digital Copy
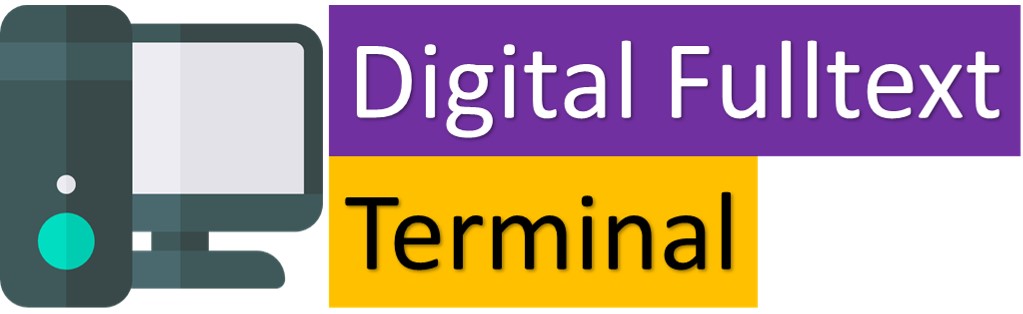
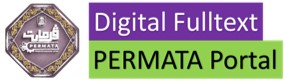
Physical Copy
ID Number
15637
Indexing
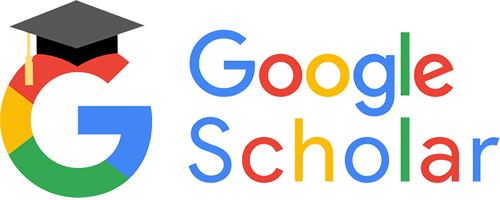
