Abstract
This study focused on optimizing the process of CNC machining to enhance productivity and product quality of surface finish Ra via the process parameters of the cutting speed (vc), feed rate (vf), and cutting depth (doc). Experimentation was performed on workpieces of AA-6061 to investigate the response Ra through variation of the process parameters to analyze their best fit using RSM with 23 full factorial designs L-8 of DOE. The analysis of variance (ANOVA) was then used to find the major contributors among them that were responsible for the Ra. Based on the result, better Ra was obtained at 0.103 μm using the best fit of vf (150 mm/min), vc (220 m/min), and doc (0.1 mm). ANOVA shows vf contributed better Ra followed by vc and doc respectively. In addition, the level of Ra’s was analyzed through contour plots represented by different colours. It continued to analyze the effect of the process parameters via the main effects plot, Pareto chart, and the contour plot in the predictive desirability model, which indicated that the plots and chart confirmed the vf had more influence compared to others. The study confirmed that the low-level parameters provided better Ra to be used for polishing.
Metadata
Item Type: | Article |
---|---|
Creators: | Creators Email / ID Num. -, Armansyah armansyah@upnvj.ac.id Nasution, Siti Rohana UNSPECIFIED Dewanto, Naufal Dary UNSPECIFIED Sudianto, Agus UNSPECIFIED Saedon, Juri UNSPECIFIED Adenan, Shahriman UNSPECIFIED |
Subjects: | T Technology > TN Mining engineering. Metallurgy > Metallurgy |
Divisions: | Universiti Teknologi MARA, Shah Alam > College of Engineering |
Journal or Publication Title: | Journal of Mechanical Engineering (JMechE) |
UiTM Journal Collections: | UiTM Journals > Journal of Mechanical Engineering (JMechE) |
ISSN: | 1823-5514 ; 2550-164X |
Volume: | 21 |
Number: | 3 |
Page Range: | pp. 145-164 |
Keywords: | Conventional CNC Machining; Surface Roughness; Aluminium Alloy; Response Surface Method; Analysis of Variance |
Date: | September 2024 |
URI: | https://ir.uitm.edu.my/id/eprint/101333 |
Download
![[thumbnail of 101333.pdf]](https://ir.uitm.edu.my/style/images/fileicons/text.png)
101333.pdf
Download (632kB)
ID Number
101333
Indexing
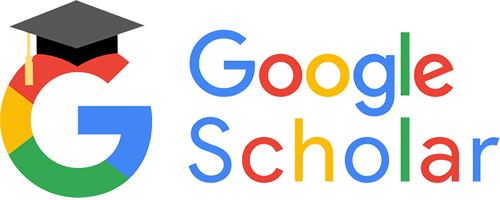
