Abstract
Since two decades ago, non-metallic composites especially honeycomb core sandwich panel were widely used in the secondary non-controlling surfaces such as the horizontal and vertical stabilizer main boxes. One of the problems in honeycomb sandwich structure is detection of delamination between the core and the skin. In order to overcome this problem, most aircraft manufacturers equipped their aircrafts with Health Monitoring System (HMS) in place to monitor the status of the aircraft structural integrity. There are many types of HMS being adopted by the aircraft manufacturers. The type of HMS being studied in this research is the one using Fiber Bragg Grating (FBG) system, which utilize optical strain sensor using light wave as the means of signal detection. The objectives of this research are to detect the location of delamination in sandwich panel and to determine the extents or the relative size of the delamination using FBG. In this study, an FBG sensor array was embedded in the honeycomb core carbon fiber skin sandwich panel. The sandwich panel was fabricated in accordance to the aviation industry standards process as well as the materials used in fabrication. The FBG’s used in the research had two sensors with grating wavelengths of 1550 nm and 1555 nm spaced approximately 100 mm between the two. The grating had a length of 15 mm. The sandwich panel had a dimension of 300 mm by 200 mm by 20 mm. The core was made from Nomex® honeycomb while the skin was made from plain weave carbon fiber supplied by Hexcel®. There were five cases being studied with different sizes of delamination were pre-introduced at different locations, using a non-stick plastic used in the vacuum bagging process, laid between the carbon fiber skin and the honeycomb core. Finite Element Analysis simulation was conducted to monitor the axial displacement at the location of the FBG’s in the specimen. The simulation was validated by experiment. The specimens underwent a 3-point bending test. The loads were applied in the increment of 0.2 kN up to 2.2 kN. The whole panel failed at the load of 2.6 kN. The data was recorded using FBG Scanner. From the simulation and experiment, there was an agreement and similarities in terms of the patterns of the result. From the research, the use of FBG was a proven method where the relative location of delamination could be detected and relative size of the delamination could be determined. The findings could be used to help monitoring the aircraft structural integrity in the area of honeycomb sandwich panel.
Metadata
Item Type: | Thesis (PhD) |
---|---|
Creators: | Creators Email / ID Num. Ramly, Ramzyzan UNSPECIFIED |
Subjects: | T Technology > TA Engineering. Civil engineering > Structural engineering > Honeycomb structure |
Divisions: | Universiti Teknologi MARA, Shah Alam > Faculty of Mechanical Engineering |
Programme: | Doctor of Philosophy |
Keywords: | Honeycomb composite; Aircraft structure; Fiber bragg |
Date: | October 2014 |
URI: | https://ir.uitm.edu.my/id/eprint/16309 |
Download
ABS_RAMZYZAN RAMLY TDRA VOL 7 IGS 15.pdf
Download (1MB) | Preview
Digital Copy
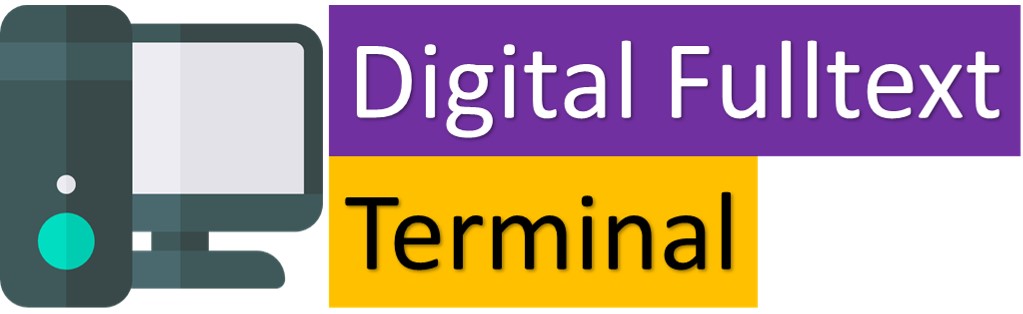
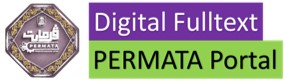
Physical Copy
ID Number
16309
Indexing
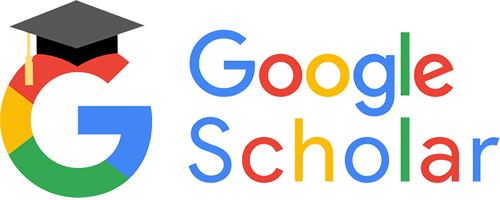
