Abstract
Composite laminates could offer excellent material properties due to their high stiffness and high strength-to-weight ratio. However, its trend of failure could lead to catastrophy due to the lack of understanding of its failure behaviour. Moreover, the accurate failure prediction of composites laminate is still yet to be established. Therefore, this study aims to predict failure of composite laminates based on multitudinous combined lamination and failure theories. The work has been conducted in five phases to cover these specific objectives; (i) to develop a MATLAB programme for failure analysis based on multitudinous combined lamination and failure theories; (ii) to compare simulated and measured extension based on ASTM D3039 (numerical versus experimental approaches) of a Carbon-Epoxy laminate under uniaxial tension; (iii) to assess the effect of different lamination scheme on the failure behaviour and mode of failure of composite laminates; (iv) to assess the effect of different lamination theories on the simulated failure behaviour of composite laminates; and finally, (v) to assess the effect of selected failure theories and determine the best fit failure theory for composite laminates. A programme was developed using MATLAB to compute the displacements, strains and stresses of the laminates based on multitudinous lamination theories (Classical Lamination Theory (CLT), First Order Shear Deformation Theory (FSDT) and High Order Shear Deformation Theory (HSDT)). For failure analysis, Maximum Stress (MS), Tsai-Wu (TW), modified Tsai-Wu (mTW), Hashin, Hoffman, Lee and Mall (MT) failure theories were employed into a programme (MATLAB) to determine the failure loads. Finite element (FE) programming (FORTRAN-90) based on HSDT was upgraded by employing the six failure theories to determine the failure loads. Failure curves are plotted and analysed. It was observed that the results from finite element simulation (ANSYS) were closer to the experimental results. However, the average difference between ANSYS and MATLAB does not exceed 1%. Deformation behaviour between lamination scheme show significant different where it was found that symmetric laminate experience elongation while anti-symmetric laminate experience twisting deformation and angle-ply laminate experience bending deformation. Determination of mode of failure using MS and mTW failure theories does not show significant different except for matrix mode of failures (anti-symmetric laminate). Comparing the FE simulation and analytical approaches, the results for uniaxial tension load (symmetric laminate) are close to each other, with a difference less than 3%. This study has proven that the developed MATLAB programme is found to be very useful for predicting failure load of composite laminate. Other than that, it is also interesting to highlight that MT failure criterion predicts smoother curve and closer to the experimental curve compared to the other five failure theories. Therefore, it can be concluded that this study has contributed significantly to enhancing knowledge about the failure prediction of composite laminates based on multitudinous combined lamination and failure theories.
Metadata
Item Type: | Thesis (PhD) |
---|---|
Creators: | Creators Email / ID Num. Samsudin, Azizul Hakim 2014646716 |
Contributors: | Contribution Name Email / ID Num. Thesis advisor Mahmud, Jamaluddin UNSPECIFIED |
Divisions: | Universiti Teknologi MARA, Shah Alam > Faculty of Mechanical Engineering |
Programme: | Doctor of Philosophy (Mechanical Engineering) – EM950 |
Keywords: | Carbon-Epoxy, ASTM D3039, MATLAB |
Date: | 2019 |
URI: | https://ir.uitm.edu.my/id/eprint/85681 |
Download
![[thumbnail of 85681.pdf]](https://ir.uitm.edu.my/style/images/fileicons/text.png)
85681.pdf
Download (105kB)
Digital Copy
Physical Copy
ID Number
85681
Indexing
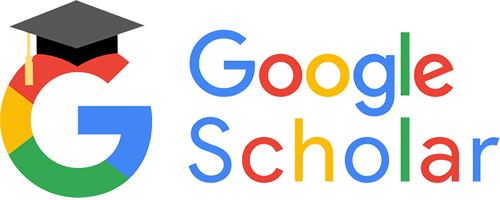
