Abstract
Turning operation plays significant role in manufacturing industry especially to fabricate machined parts. Meanwhile surface quality is one of the important aspects to measure the performance of lathe machine. This research experimentally investigated the effect of turning parameters which are feed rate, cutting speed and depth of cut toward surface roughness and machining time by using Response Surface Methodology (RSM). Central Composite Design (CCD) was chosen to design 15 set of experiments for 3 continuous factors. The mild steel was chosen as work material and had been turning under hot facing operation on conventional JET Lathe machine. The cutting tool used for this experiment was Tungsten Carbide insert. The experimental results were analyzed using a statistical Analysis of Variance (ANOVA) and developed mathematical model for surface roughness. With accuracy of 94.3% by compared experimental and theoretical data, the model can be verified as valid. The results indicate that feed rate give most influence factor to the surface roughness rather than cutting speed and depth of cut. Furthermore, for optimize condition, maximum cutting speed, minimum feed rate and depth of cut can increase the surface quality of machined parts. In addition, the analysis also generated the relationship between cutting parameters and machining time. It is show that the feed rate and cutting speed influenced the machining time.
Metadata
Item Type: | Student Project |
---|---|
Creators: | Creators Email / ID Num. Mohamad Fuad, Muhammad Fikri 2014201396 |
Subjects: | T Technology > TJ Mechanical engineering and machinery T Technology > TJ Mechanical engineering and machinery > Control engineering systems. Automatic machinery (General) |
Divisions: | Universiti Teknologi MARA, Pulau Pinang > Permatang Pauh Campus > Faculty of Mechanical Engineering |
Programme: | Bachelor Of Mechanical Engineering (Manufacturing) (Hons.) |
Keywords: | fabricate machined parts, Aerospace Industries, Central Composite Design |
Date: | July 2017 |
URI: | https://ir.uitm.edu.my/id/eprint/31435 |
Download
![[thumbnail of 31435.pdf]](https://ir.uitm.edu.my/style/images/fileicons/text.png)
31435.pdf
Download (99kB)
Digital Copy
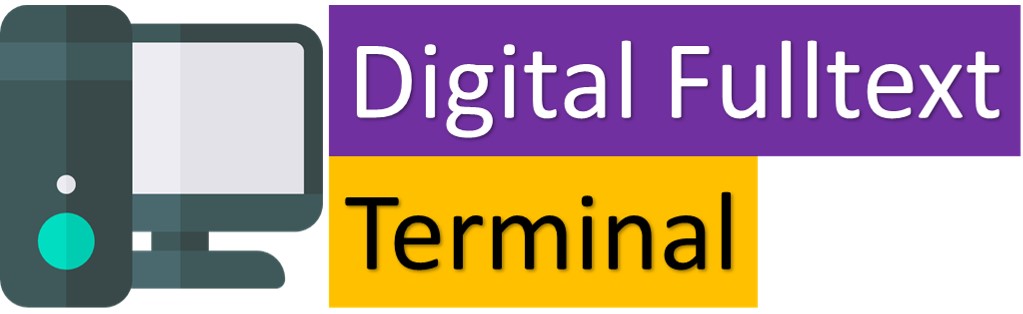
Physical Copy

ID Number
31435
Indexing
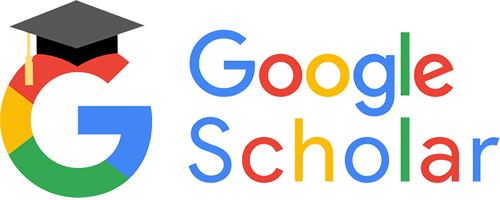
