Abstract
The primary objective of this study is probe into the level of implementation of OSH A in SMIs - food-manufacturing factories, which located in Kedah. In this context, the main aim is to determine factors related to the implementation of OSHA in the workplace. Factors that are under the scope of this study are the management commitment and involvement, the level of employee compliance with OSH, employees' perceptions towards the implementation and effectiveness of company’s safety programmes, workplace accident occurrences, company compliance with the safety regulations, training activity, and respondent personal attributes. Data were collected from 256 employees in mid-July - mid September 2004. Generally, the level of OSH practices and implementation in these food manufacturing is at an acceptable level. From the employee’s point of view, generally three aspects of the OSH practices are within the acceptable level. Some of the employees experienced accidents at their workplaces, but a majority of them had encountered slight injuries. Findings indicated that a majority of the accidents is caused by human factors, and employers seldom took serious actions against those involved in workplace accident, as warning is the most frequent mentioned action taken by employers. Besides that, small cut was identified as the majority type of accident that occurred in the SMIs for the past two years. Result also suggested that these SMIs' employers have taken food safety seriously as safety glove and mask are the most frequent mentioned types of personnel protective equipment provided by employers. However, the culture of occupational safety and health practices need to be cultivate and enhance seriously in these organization, as findings have indicated that many of the employers are less interested in given out incentives when their employees comply with all the safety rules and regulations. In terms of the kinds of punishment that an employee would receive if he/she does not comply with safety rules, the most frequent mentioned punishment was "warning". Results also suggested that a majority of the employers provided their employees with task-related training and employers most preferred providing special pamphlet /regulations, holding briefing and talk session to enhance the employees’ OSH awareness and practices. Besides, few personal attributes have implications on OSH implementation. Research suggested that the success of OSH implementation relied on the co-operation of many parties, in particular the employers, employees and enforcement bodies.
Metadata
Item Type: | Research Reports |
---|---|
Creators: | Creators Email / ID Num. Hussin, Zaliha UNSPECIFIED Ju, Soon Yew UNSPECIFIED Zakaria, Zaherawati UNSPECIFIED |
Subjects: | H Social Sciences > HD Industries. Land use. Labor > Small business. Medium-sized business H Social Sciences > HD Industries. Land use. Labor > Management. Industrial Management |
Divisions: | Universiti Teknologi MARA, Kedah > Sg Petani Campus > Research Management Institute (RMI), UiTM Cawangan Kedah |
Keywords: | Food-Manufacturing; OSHA; Workplace; Food Safety |
Date: | March 2005 |
URI: | https://ir.uitm.edu.my/id/eprint/26623 |
Download
![[thumbnail of LP_ZALIHA HJ. HUSSIN RMI K 05_5.pdf]](https://ir.uitm.edu.my/style/images/fileicons/text.png)
LP_ZALIHA HJ. HUSSIN RMI K 05_5.pdf
Download (199kB)
Digital Copy
Physical Copy
ID Number
26623
Indexing
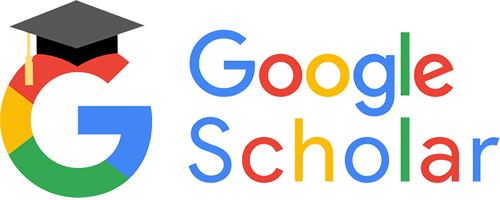
