Abstract
Sheet metal forming is a common manufacturing practice adopted by the Malaysian automotive industries to form various shapes involving processes such as blanking, piercing, bending, drawing, etc. The formability of sheet metal parts depends very much on the material properties, machine and process parameters and part geometry. This project provides an insight into drawing of low carbon steel axis-symmetrical cylindrical cup using finite element analysis (FEA) that generates the forming limit diagram (FLD) of the part to describe its formability. The DYNAFORM as the FEA simulation software tool evaluates the forming limit strains and thickness of the drawn circular cup. The behavior of the actual drawn part was in good agreement with the simulation results. Concurrently, several process parameters were identified as input factors to carry out the Design of Experiments (DOE) process. The initial process parameters namely the blank holder force (BHF), die and punch radius, and friction of coefficient were selected with their respective maximum and minimum levels to fit into the Research Surface Methodology (RSM) design model. The RSM method was employed to identify the relative influence of each process parameters considered in this study. The Box- Behnken BB (3) design was selected and refining the model was done using the CC (2³) (Central Composite Design) design. Based on the predicted thickness distribution (numerical simulation) of the drawn circular cup and the analysis of variance (ANOVA) test, it is evident that the punch/die radius has the greatest influence on the quality characteristic of the drawn low carbon steel blank sheet followed by the BHF and the friction of coefficient. The derived mathematical model for the response was found to fit significantly in predicting the data. The integration of finite element method (simulation) and RSM technique (mathematical modeling) acts as a favorable tool to predict the influence of the process parameters selected. The error range between the actual (numerical simulation) and the predicted values for the attainment of maximum thickness is less than 8% after optimization. It can be concluded that the RSM adapted as mathematical modeling for sheet metal drawing optimization is reasonably accurate and can be used for prediction of thickness variation within the limits of the factors investigated.
Metadata
Item Type: | Research Reports |
---|---|
Creators: | Creators Email / ID Num. Omar, Abdul Rahman UNSPECIFIED |
Subjects: | T Technology > TJ Mechanical engineering and machinery > Mechanical movements T Technology > TJ Mechanical engineering and machinery > Control engineering systems. Automatic machinery (General) |
Divisions: | Universiti Teknologi MARA, Shah Alam > Research Management Centre (RMC) |
Keywords: | Stamping die; Response surface; methodology method |
Date: | 2011 |
URI: | https://ir.uitm.edu.my/id/eprint/16863 |
Download
![[thumbnail of LP_ABDUL RAHMAN OMAR RMI 11_5.pdf]](https://ir.uitm.edu.my/style/images/fileicons/text.png)
LP_ABDUL RAHMAN OMAR RMI 11_5.pdf
Download (3MB)
Digital Copy
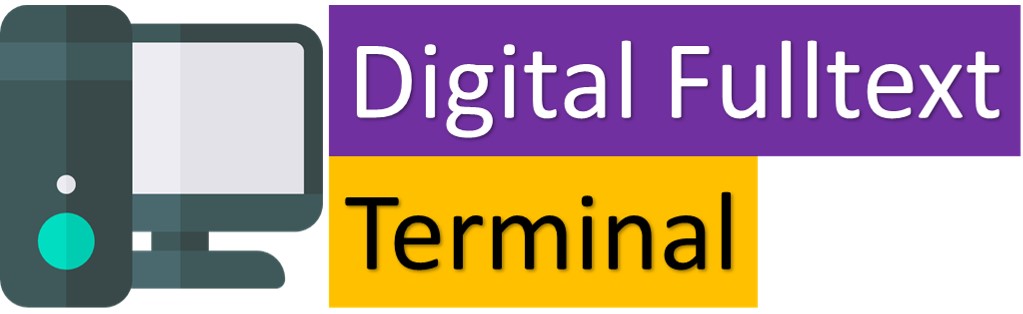
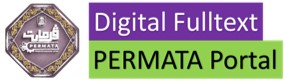
Physical Copy
ID Number
16863
Indexing
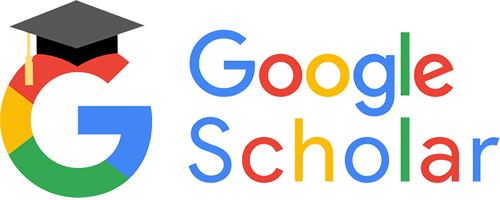
